MP&C
Member
Well time to finish up Randy's scooter fender(s). The original (rear) had been loose at some point as the fender mounting holes were nice and elongated from flopping around. So I'll get them filled in and Randy will need to match drill them to the frame..
Use the right tools for the job :headscrat
After marking, when cutting out such a small piece I like to leave a "handle" until the very end..
....gives you something to hold onto while fine tuning the fit
Nice and snug....
Tacking in the filler piece...
Next was to trim a nice radius on the front and back ends of the new front fender....
Last on the list, the forming process with the old fender left some "pie crust" edging, as seen here and in an original photo...
So we needed a special tool in order to duplicate this feature...
Spacing all marked out....
Finished edge...
All ready for delivery!

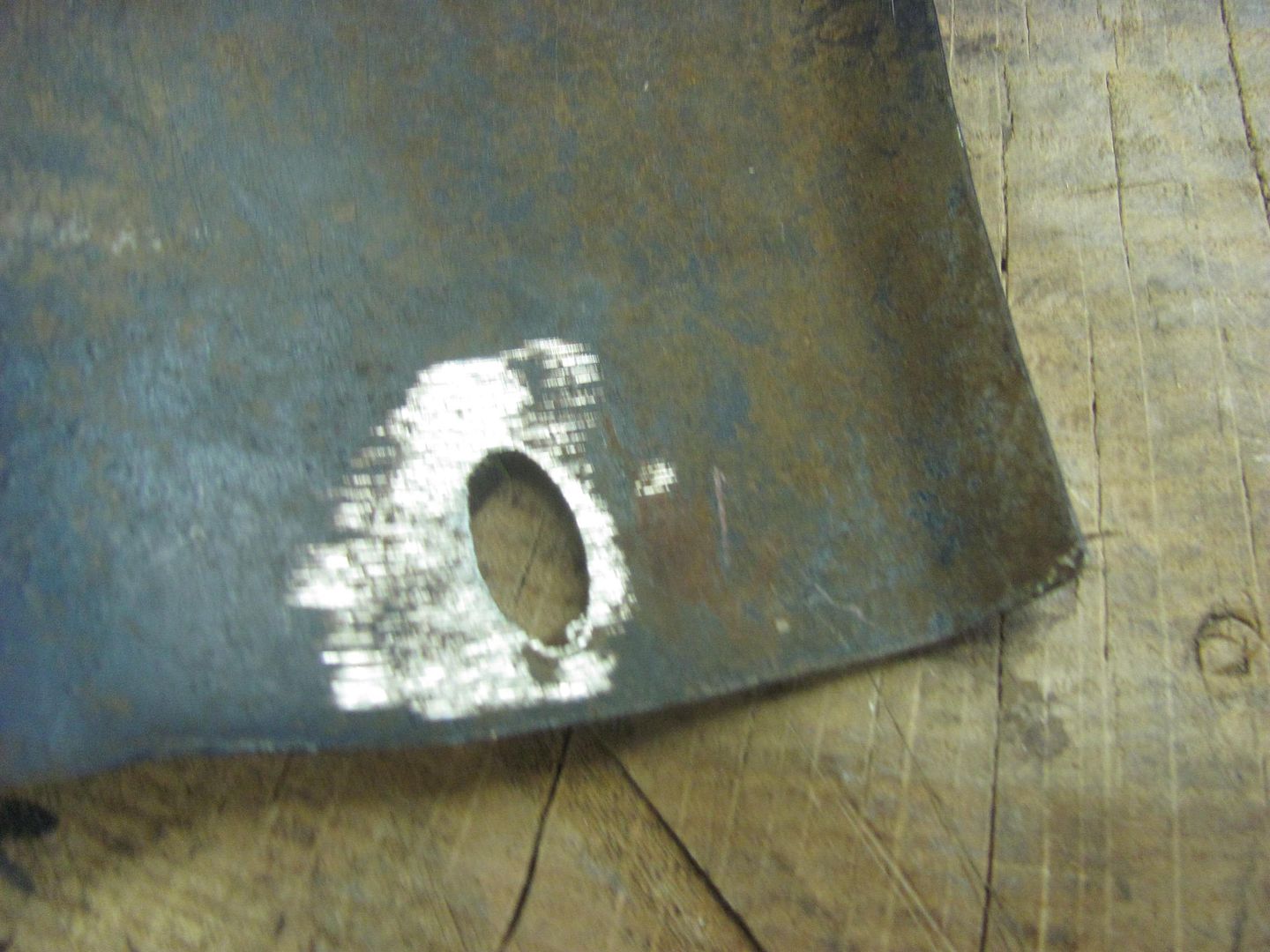
Use the right tools for the job :headscrat
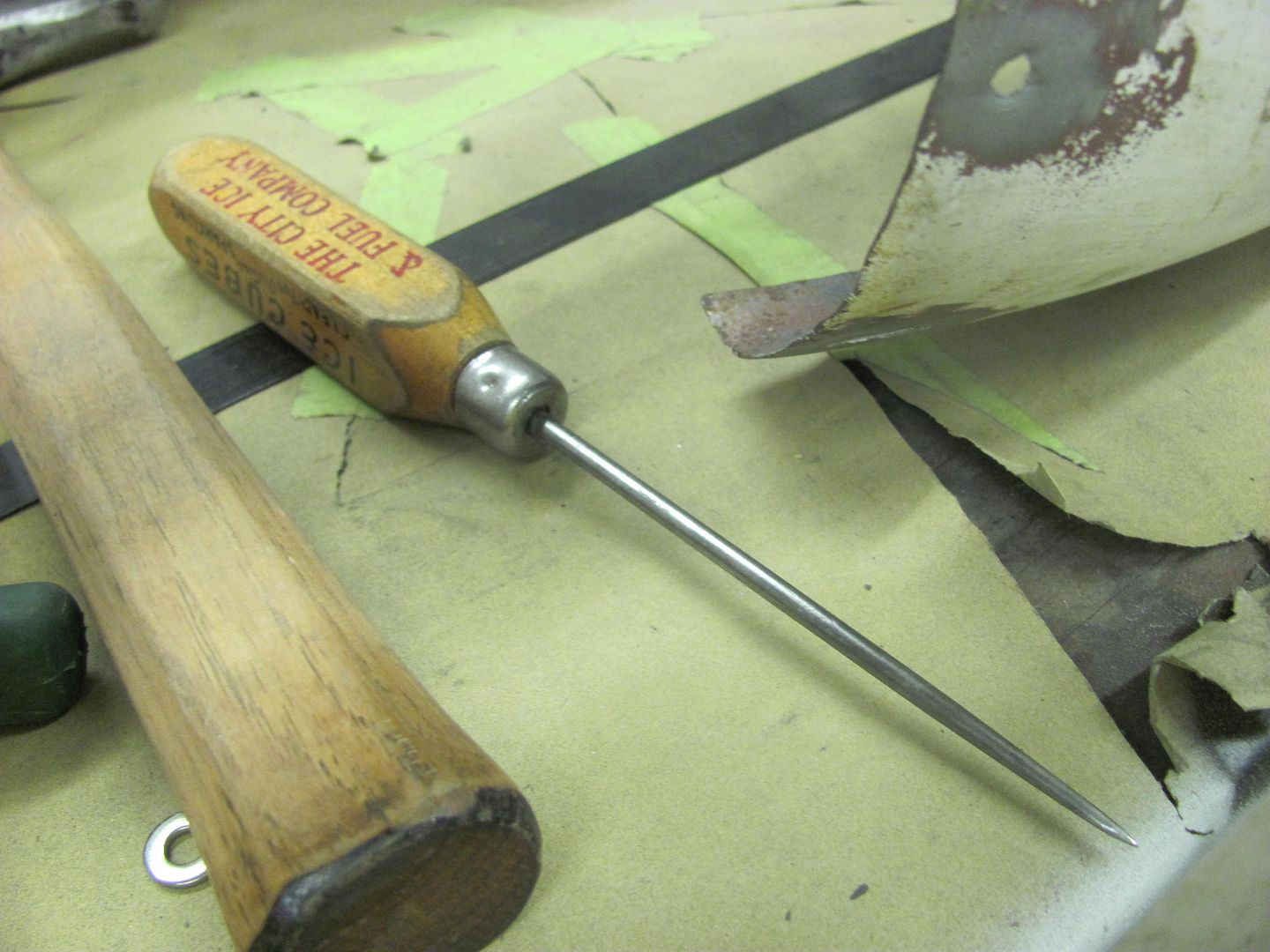
After marking, when cutting out such a small piece I like to leave a "handle" until the very end..
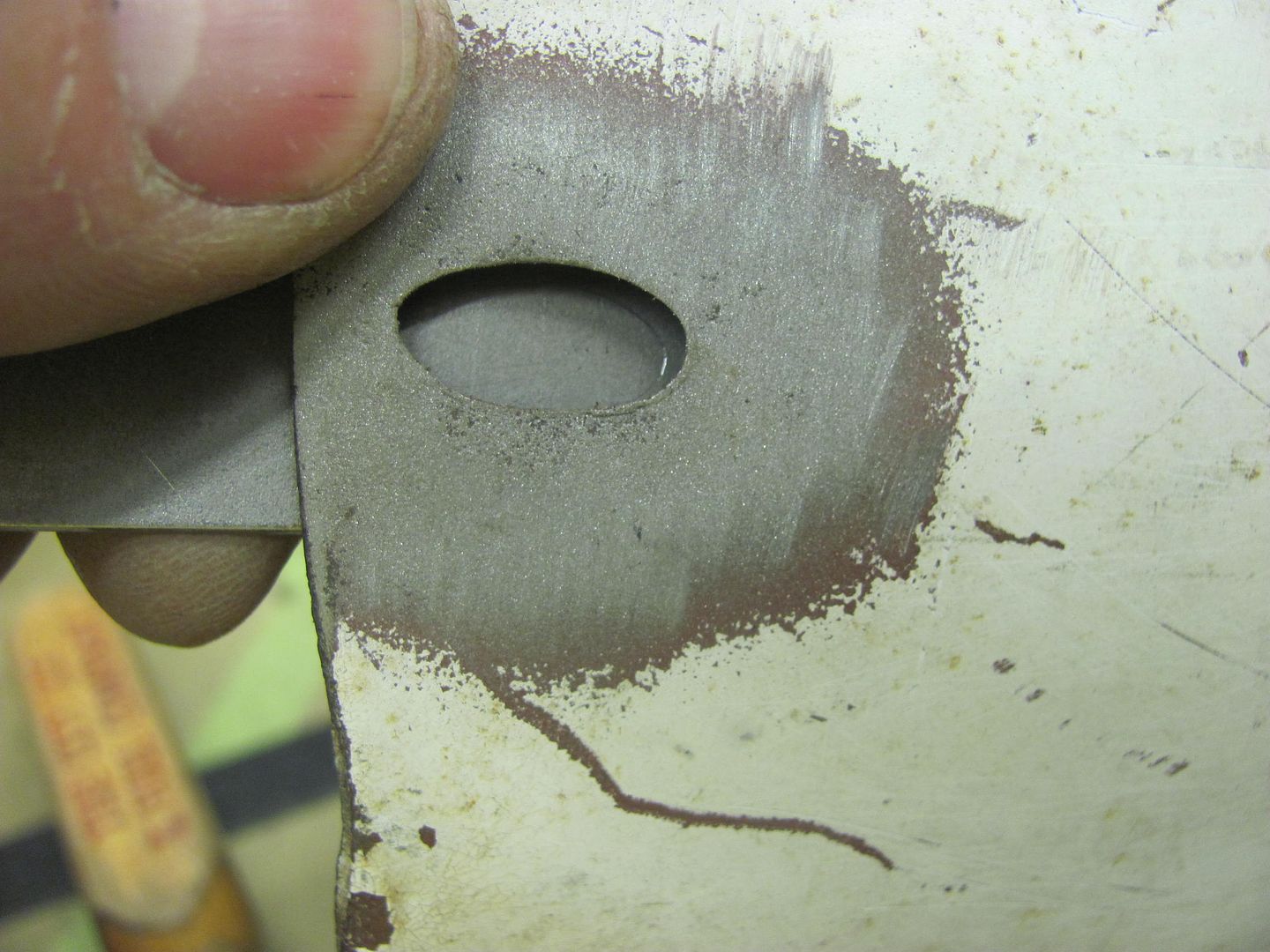
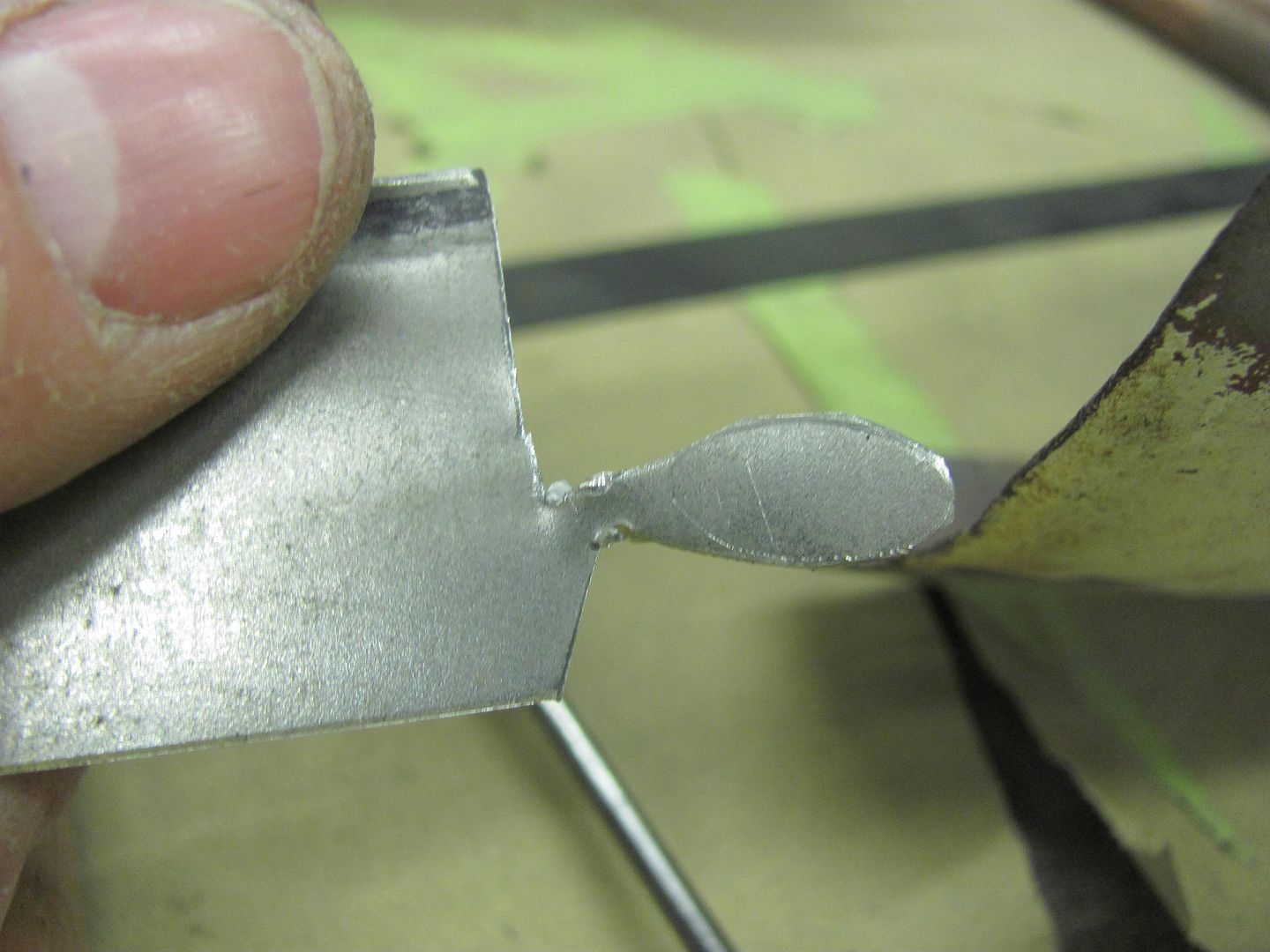
....gives you something to hold onto while fine tuning the fit
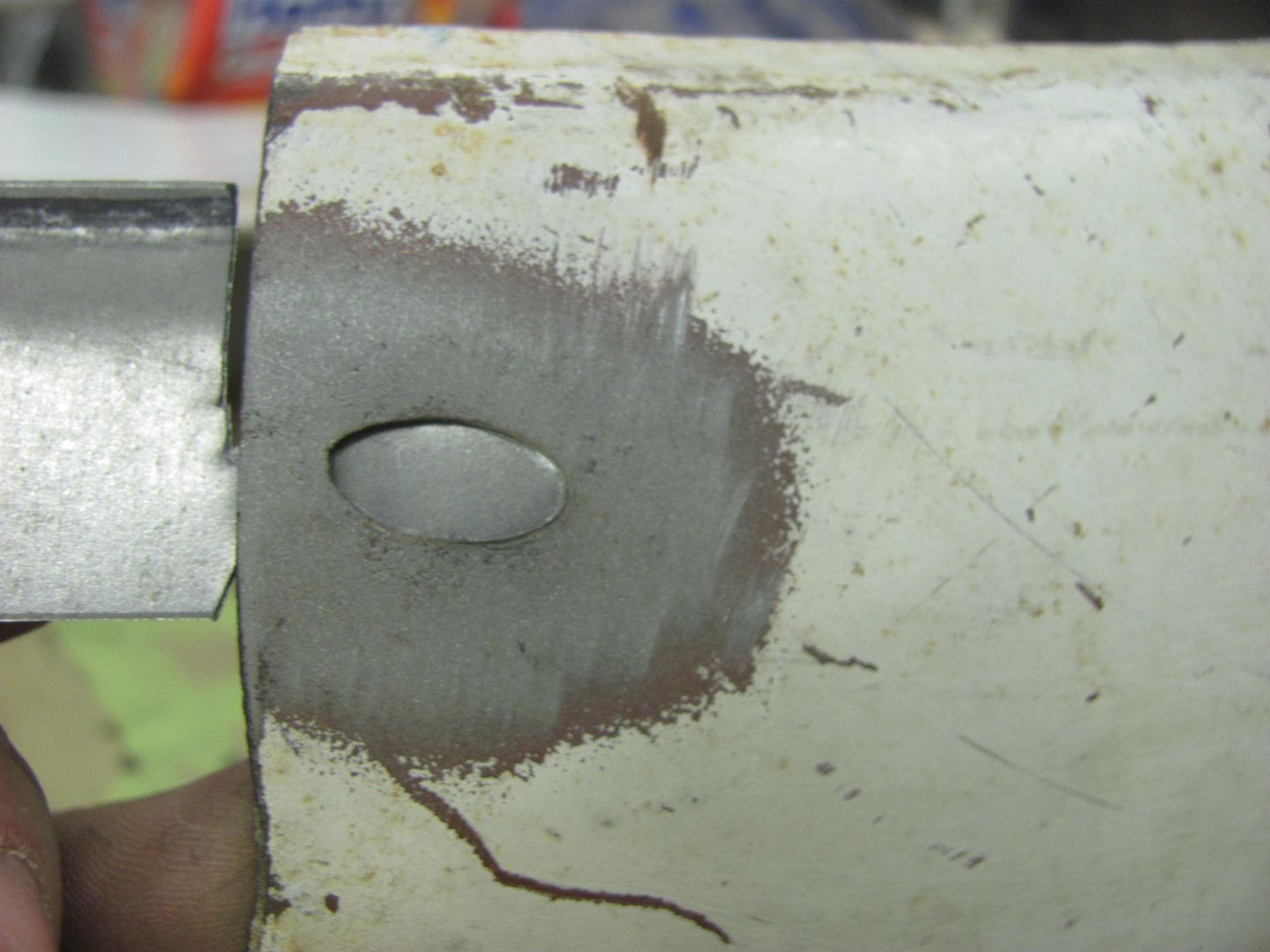
Nice and snug....
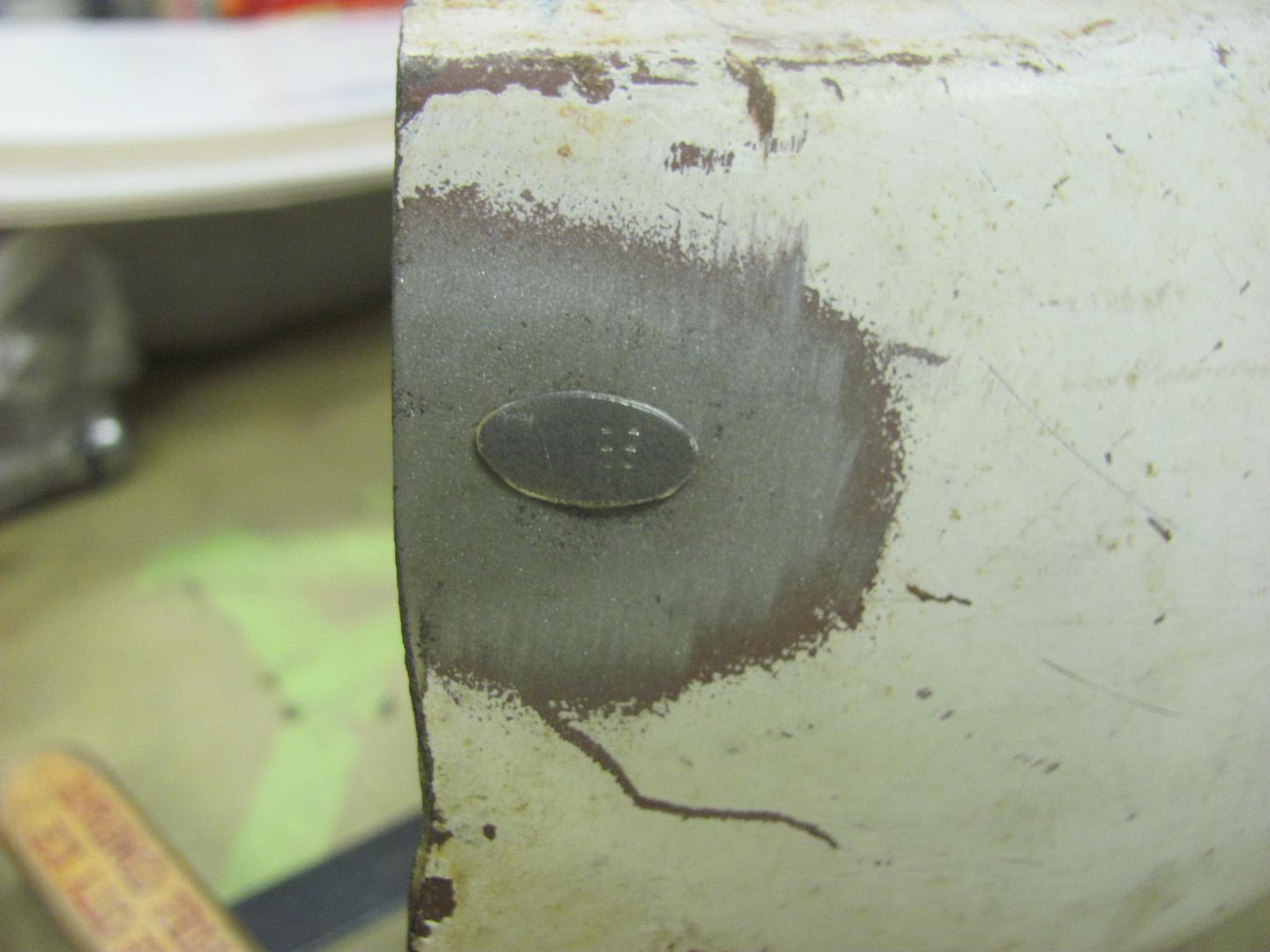
Tacking in the filler piece...
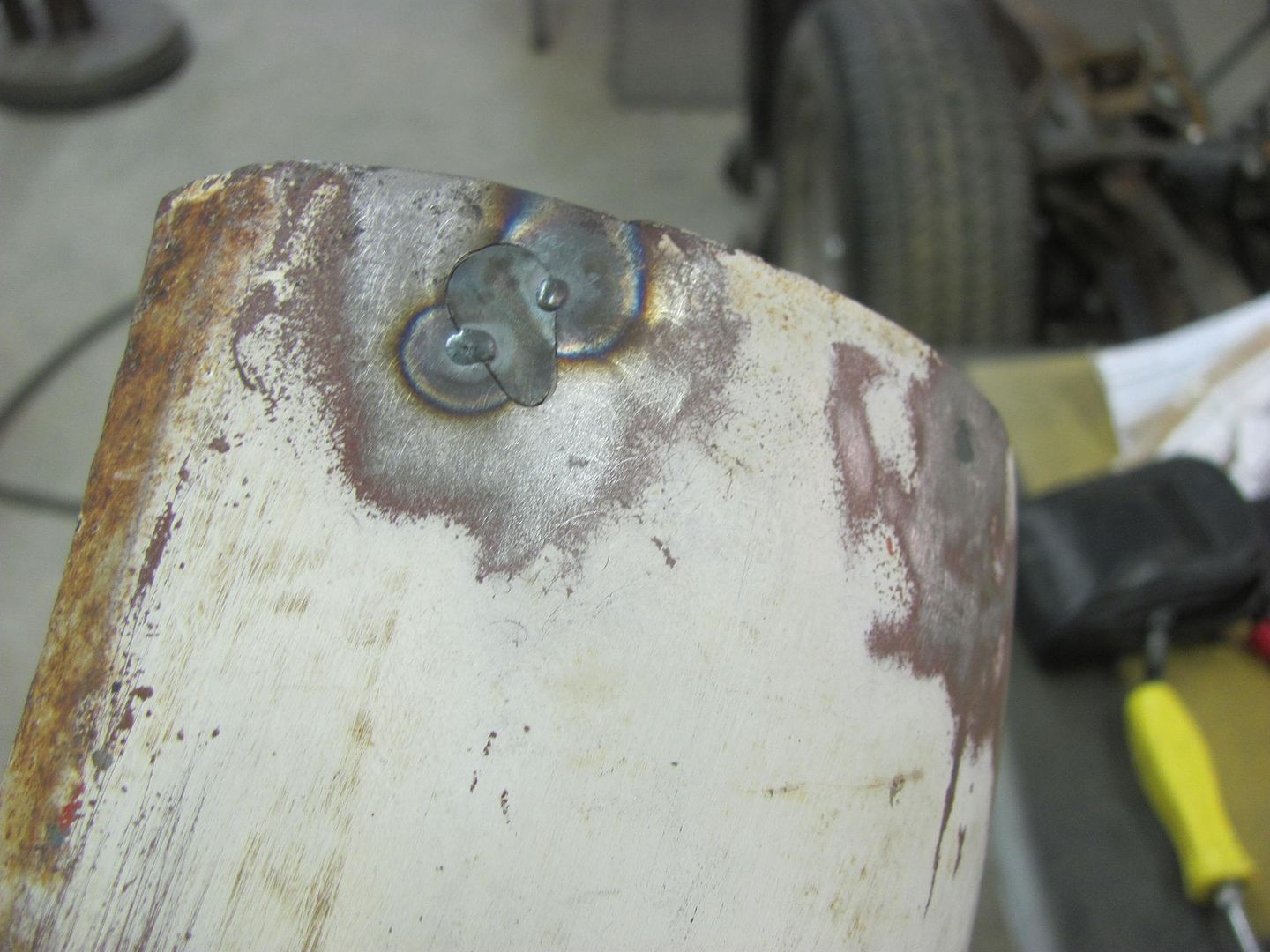
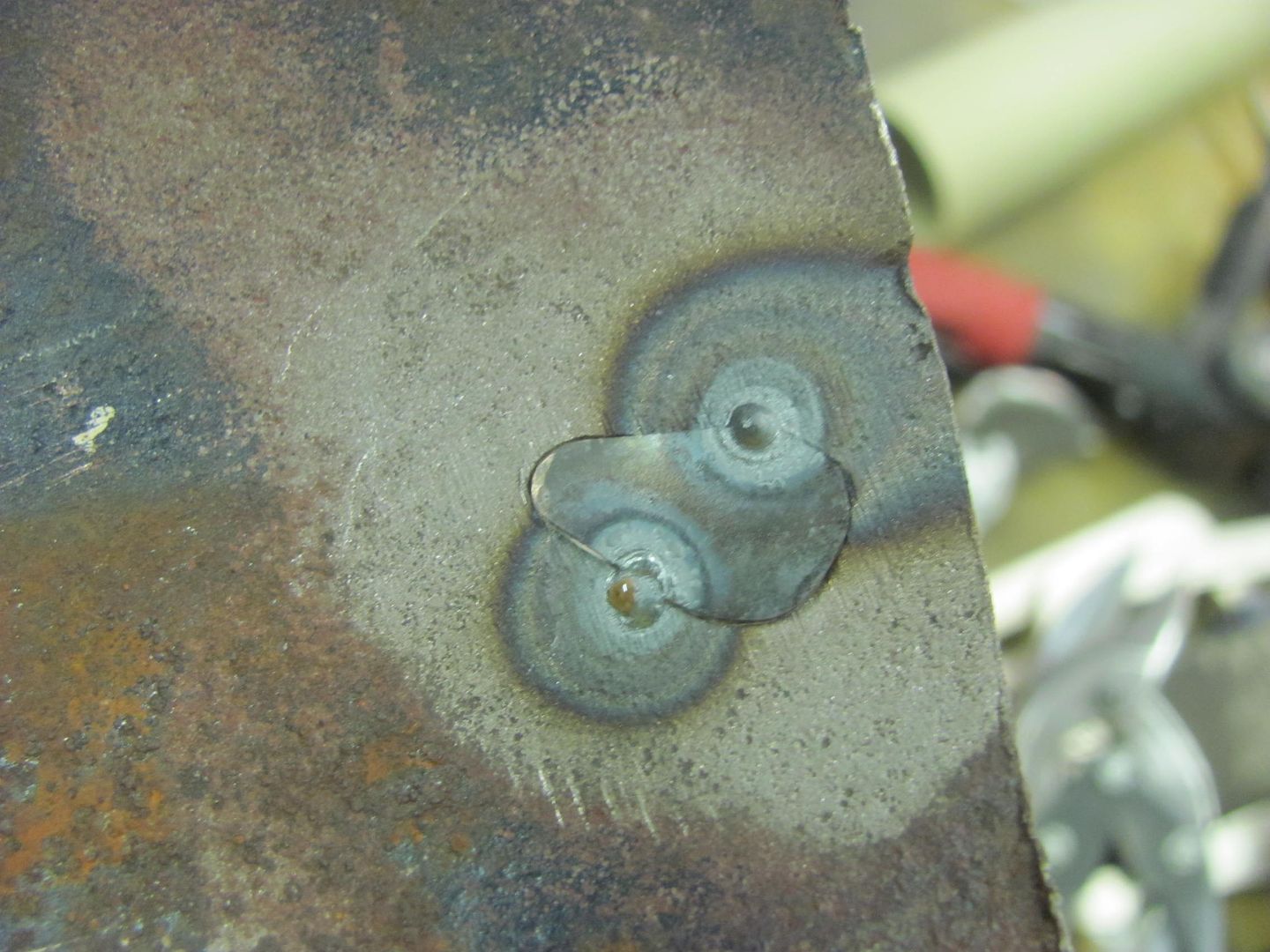
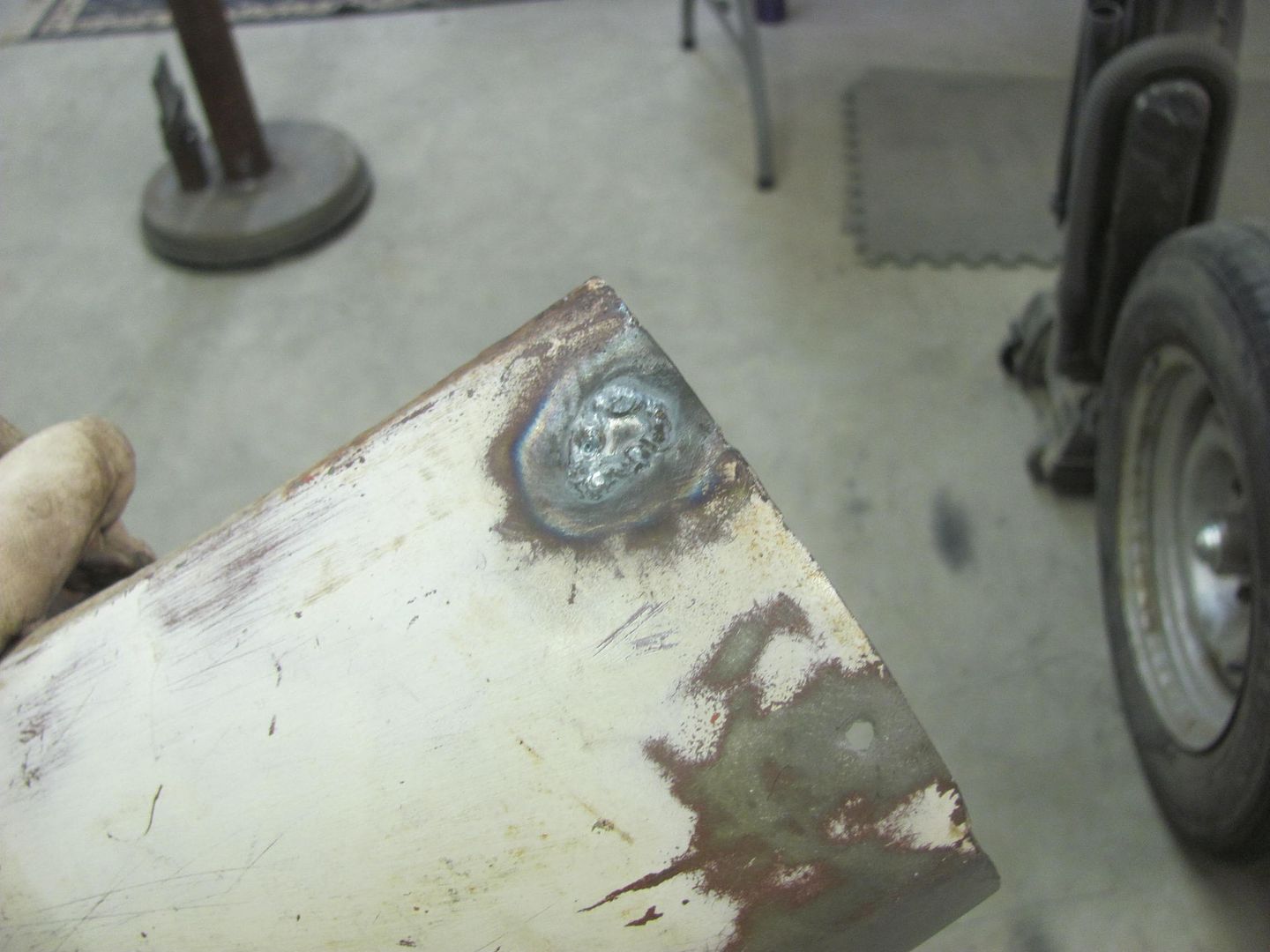
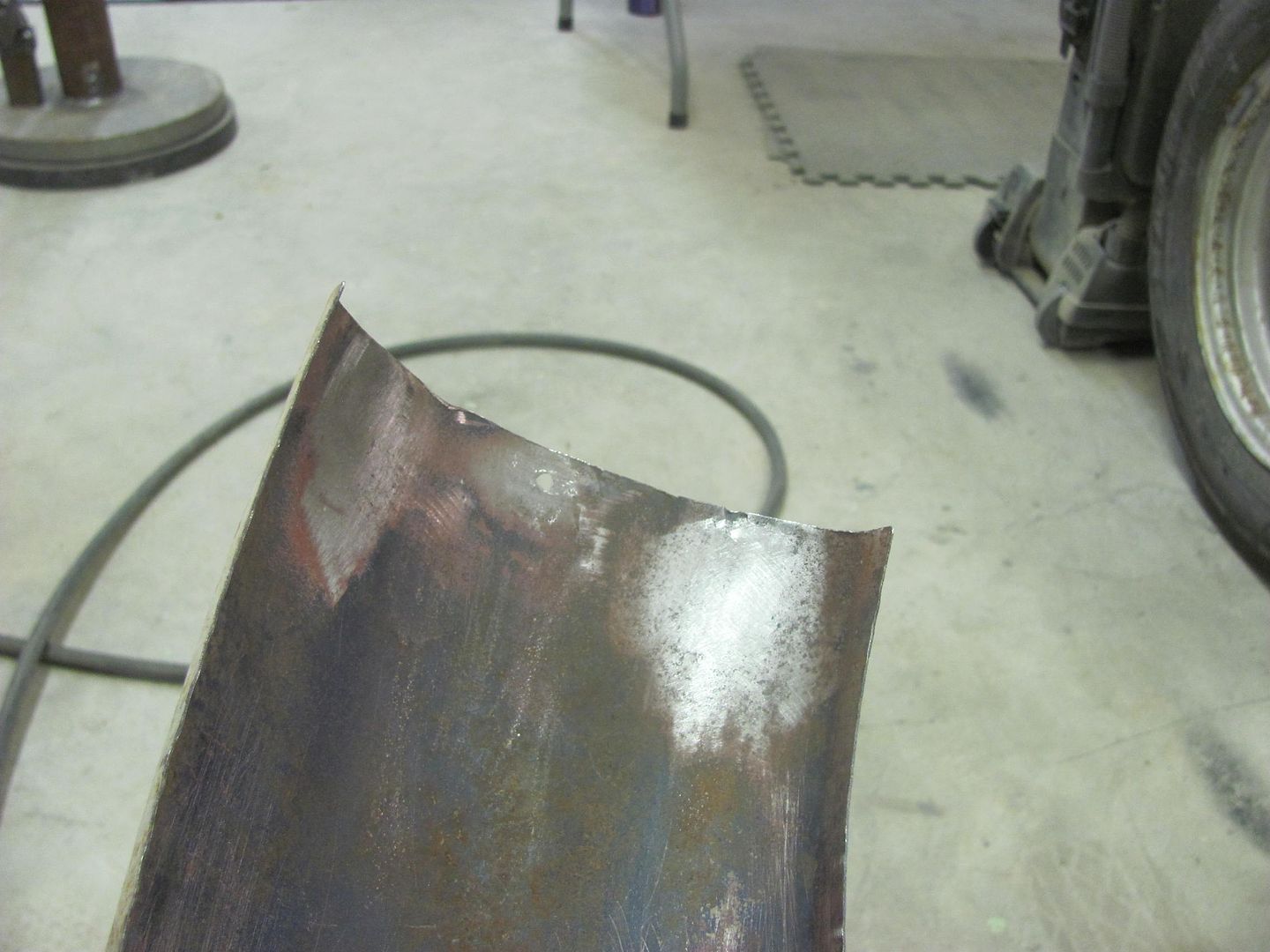
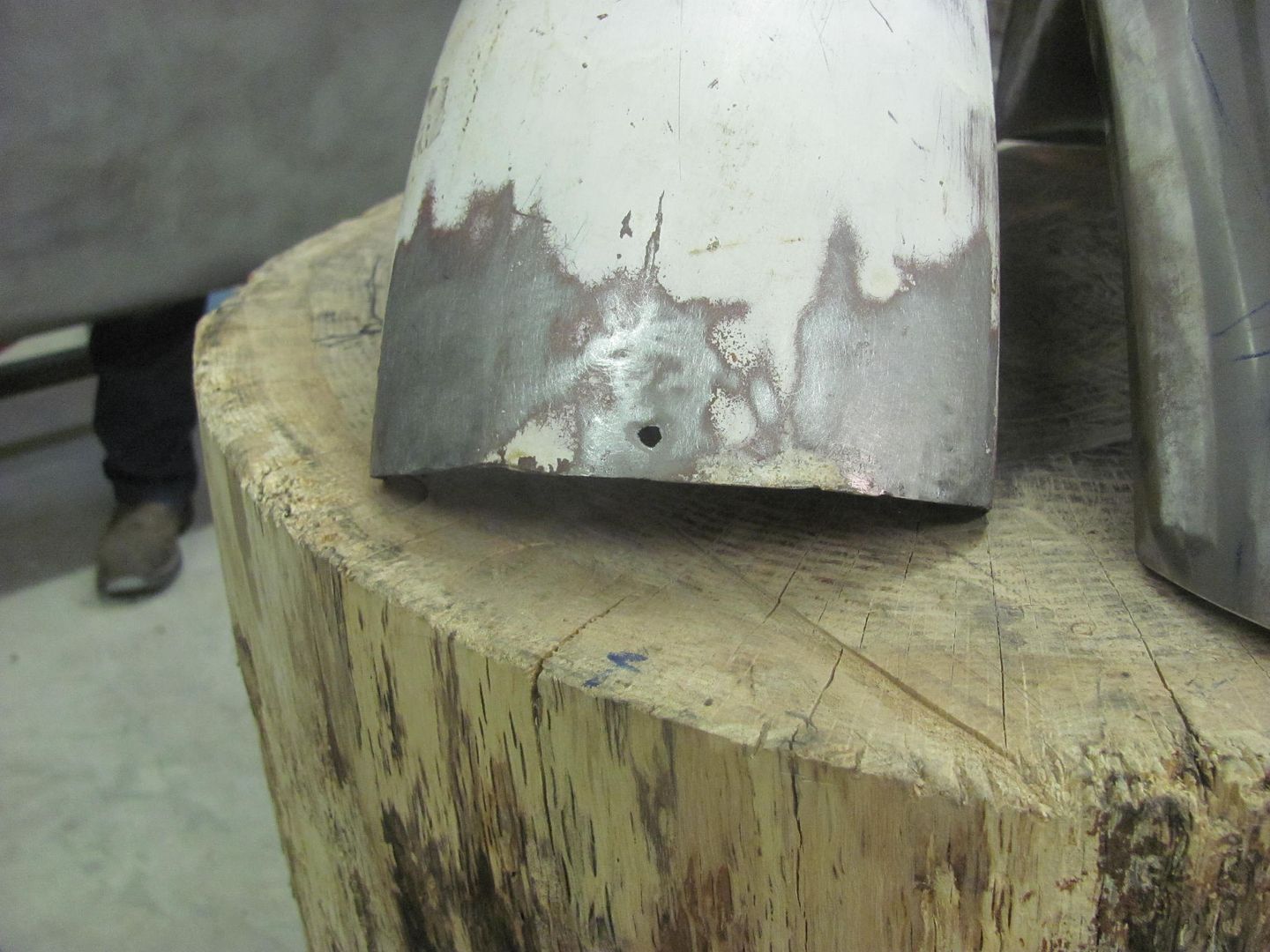
Next was to trim a nice radius on the front and back ends of the new front fender....
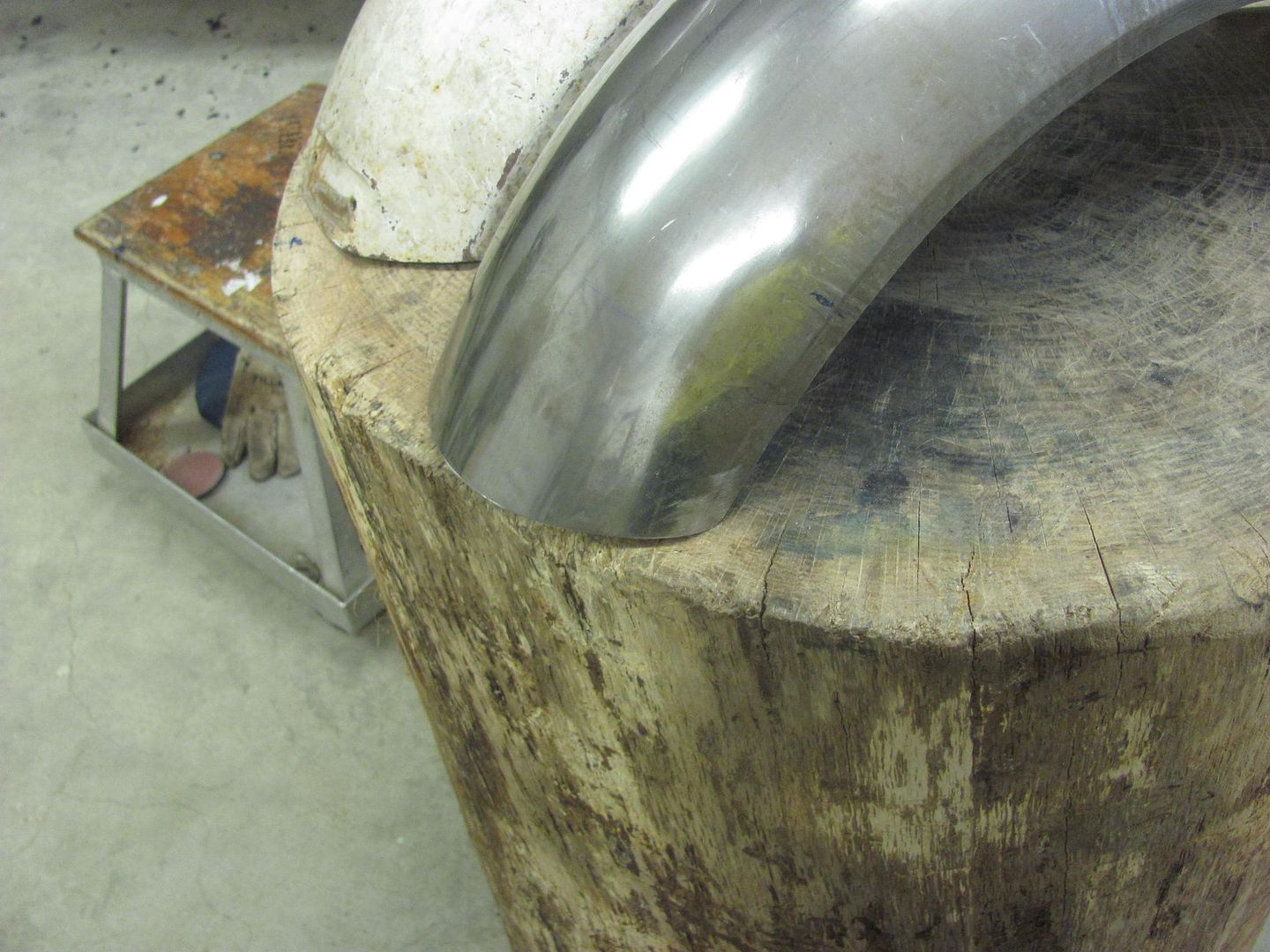
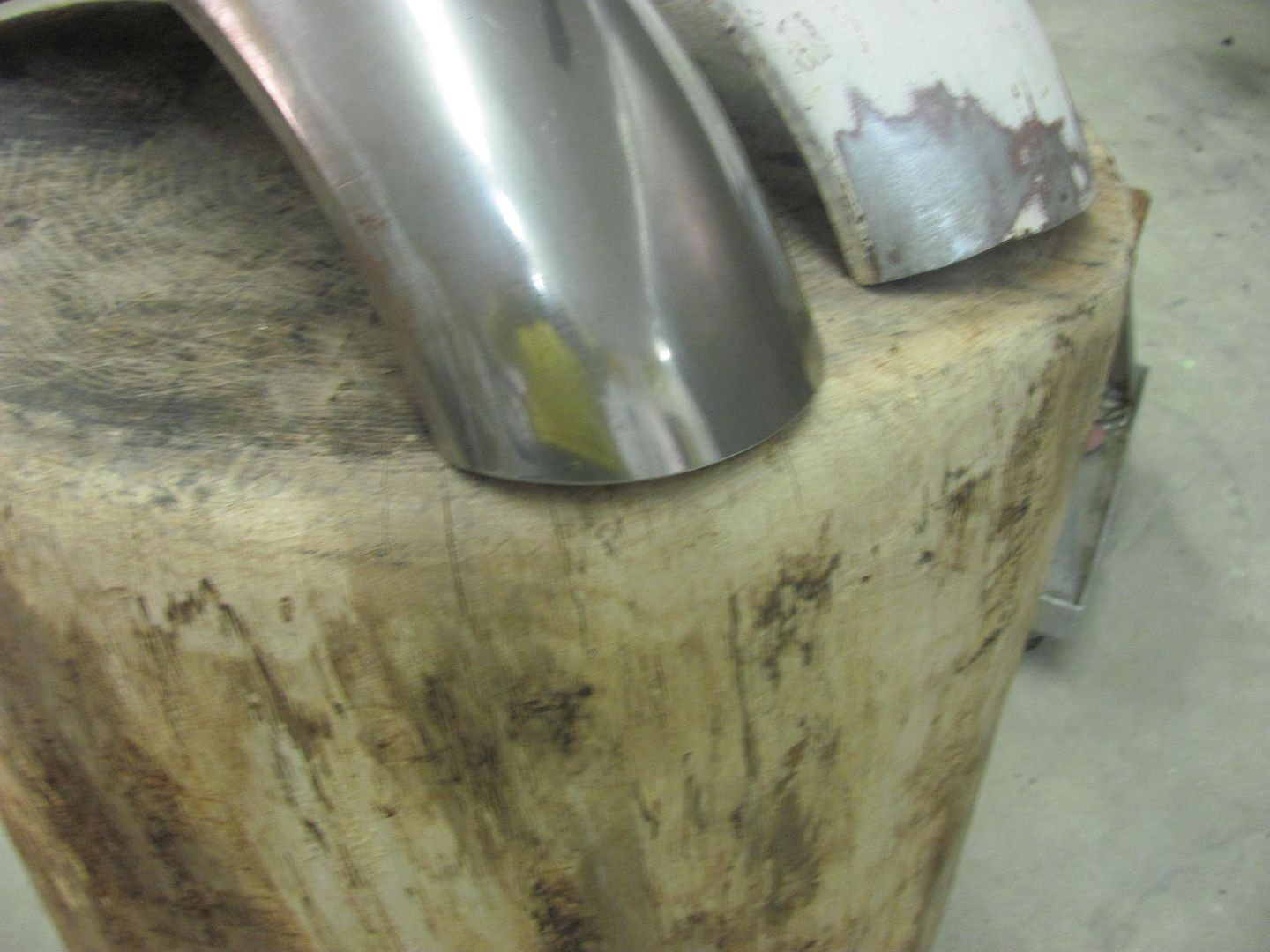
Last on the list, the forming process with the old fender left some "pie crust" edging, as seen here and in an original photo...
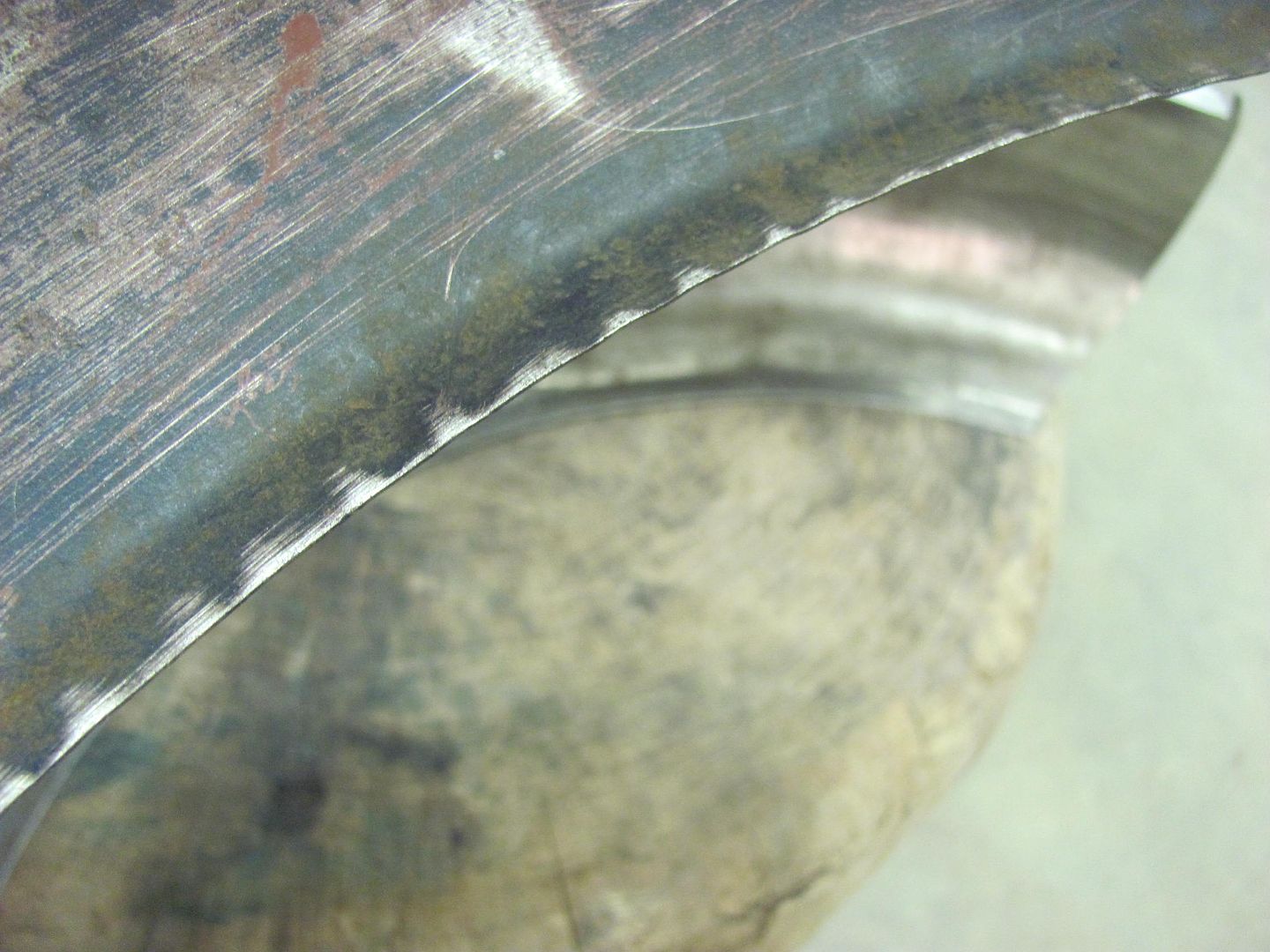
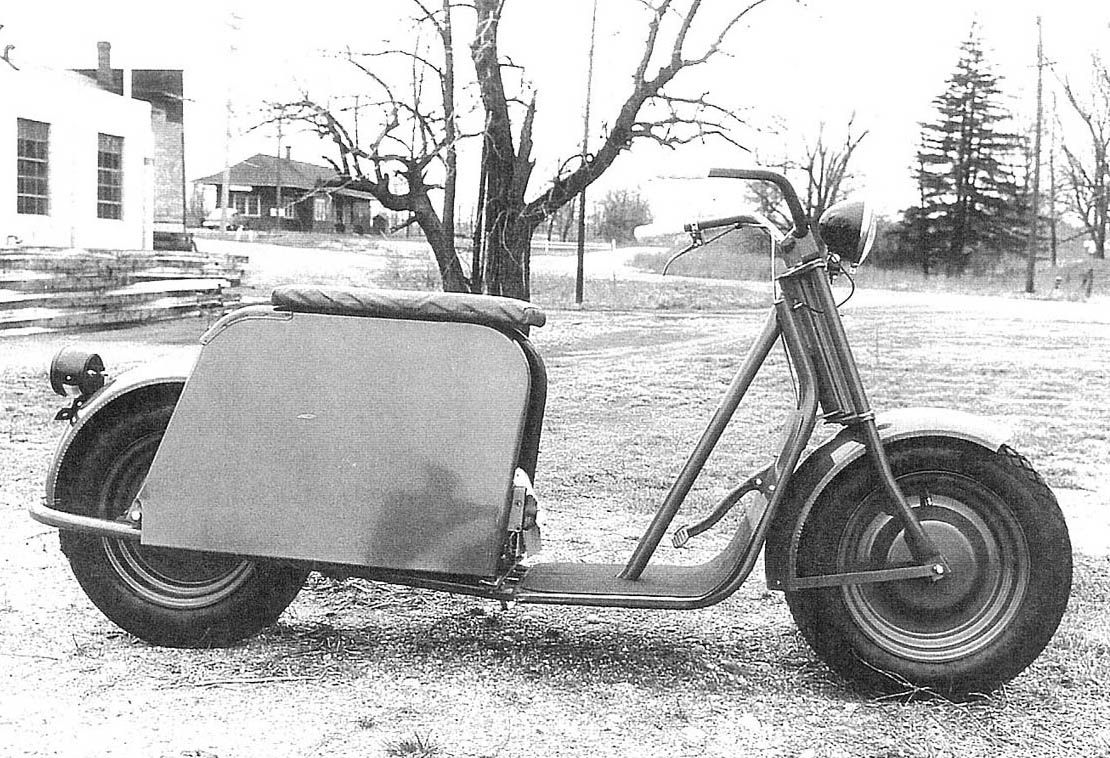
So we needed a special tool in order to duplicate this feature...
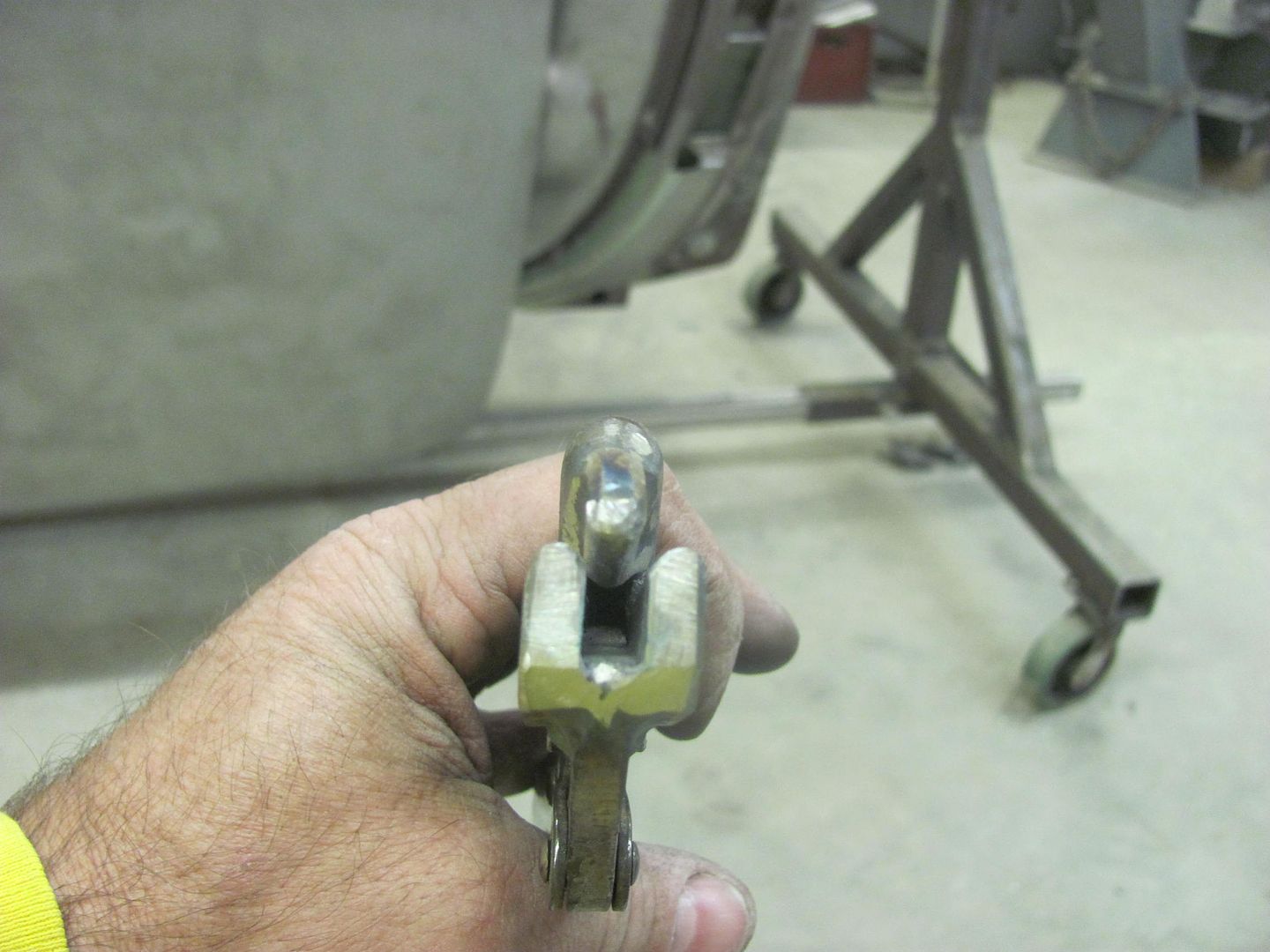
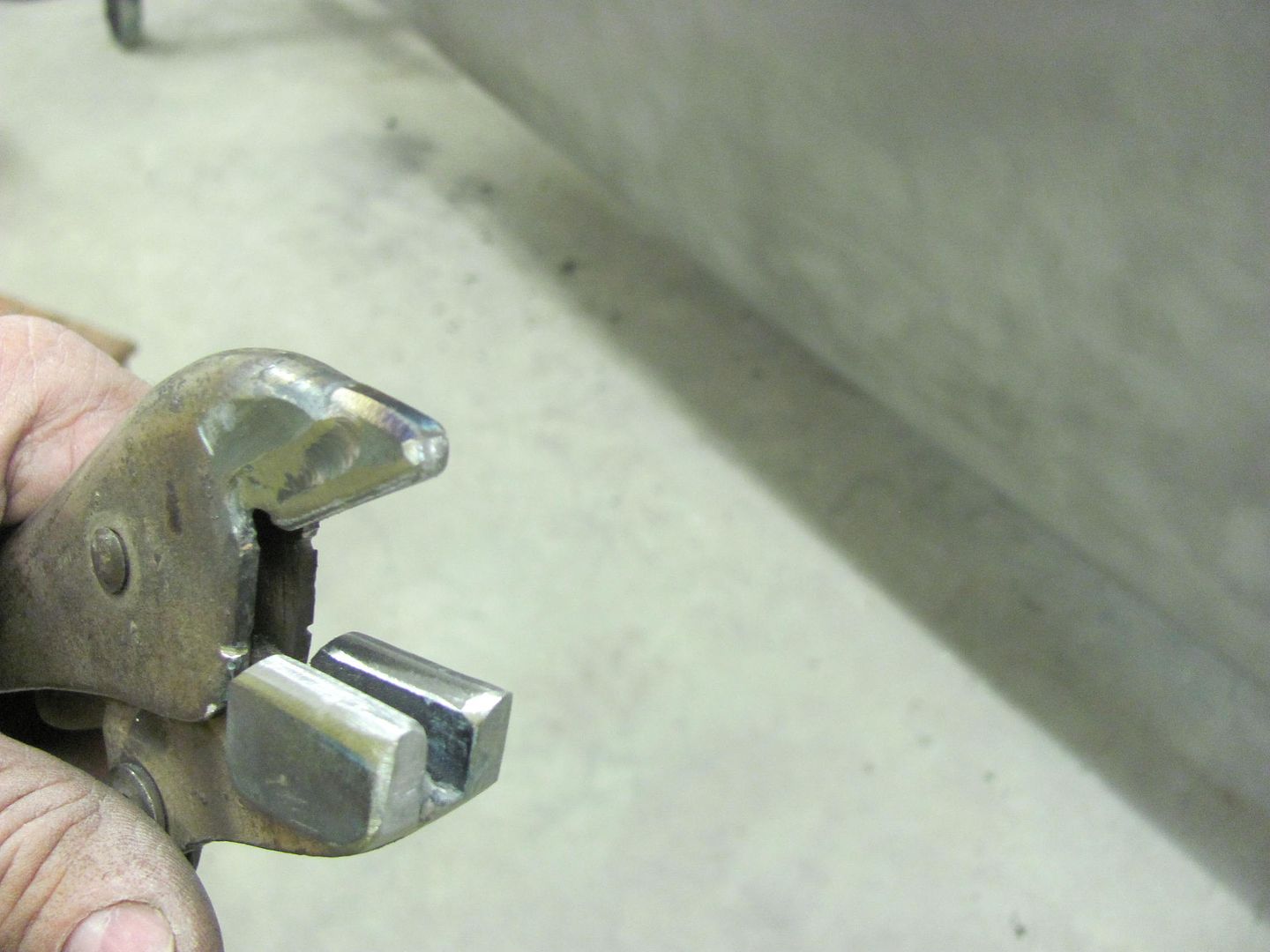
Spacing all marked out....
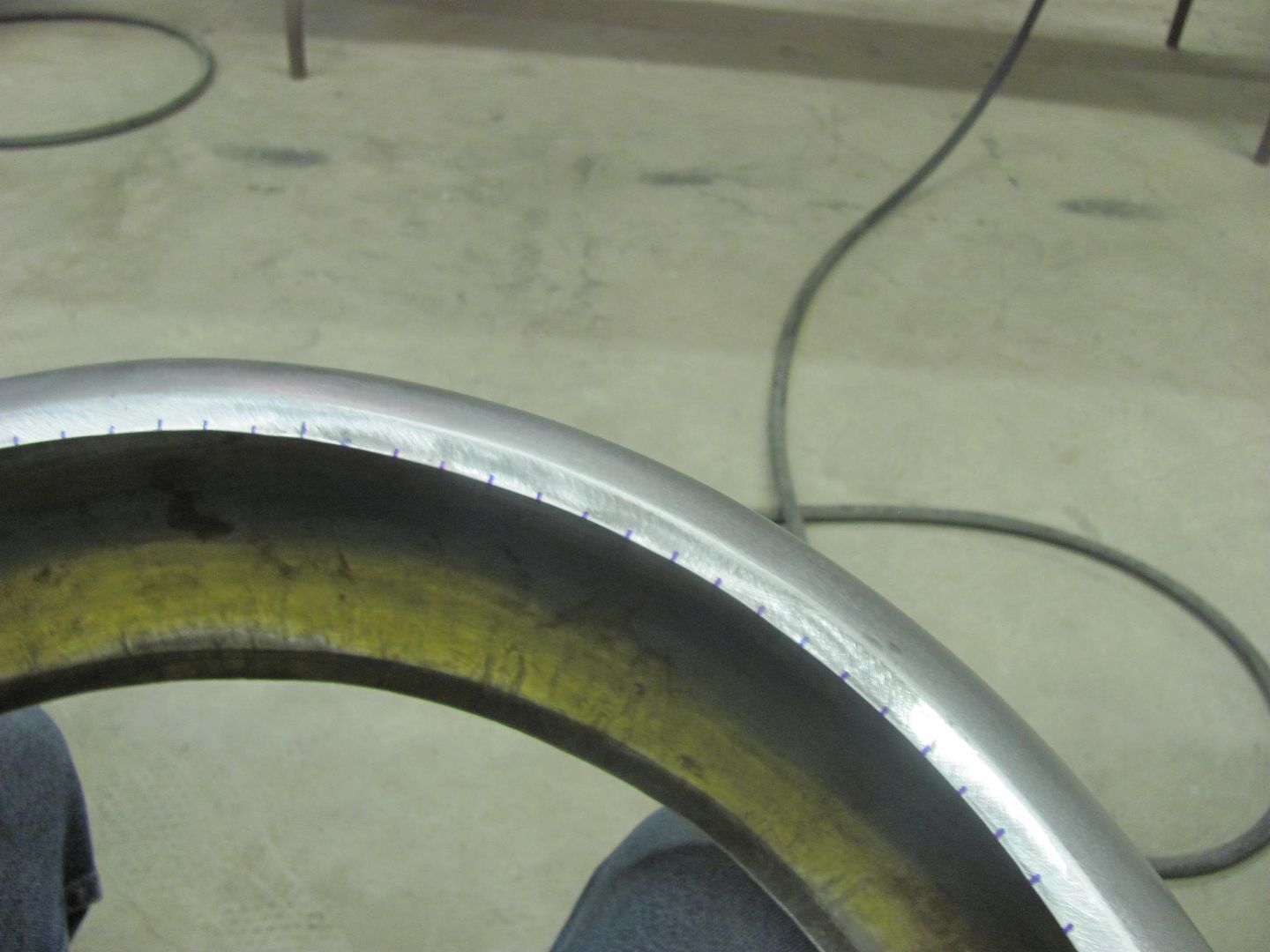
Finished edge...
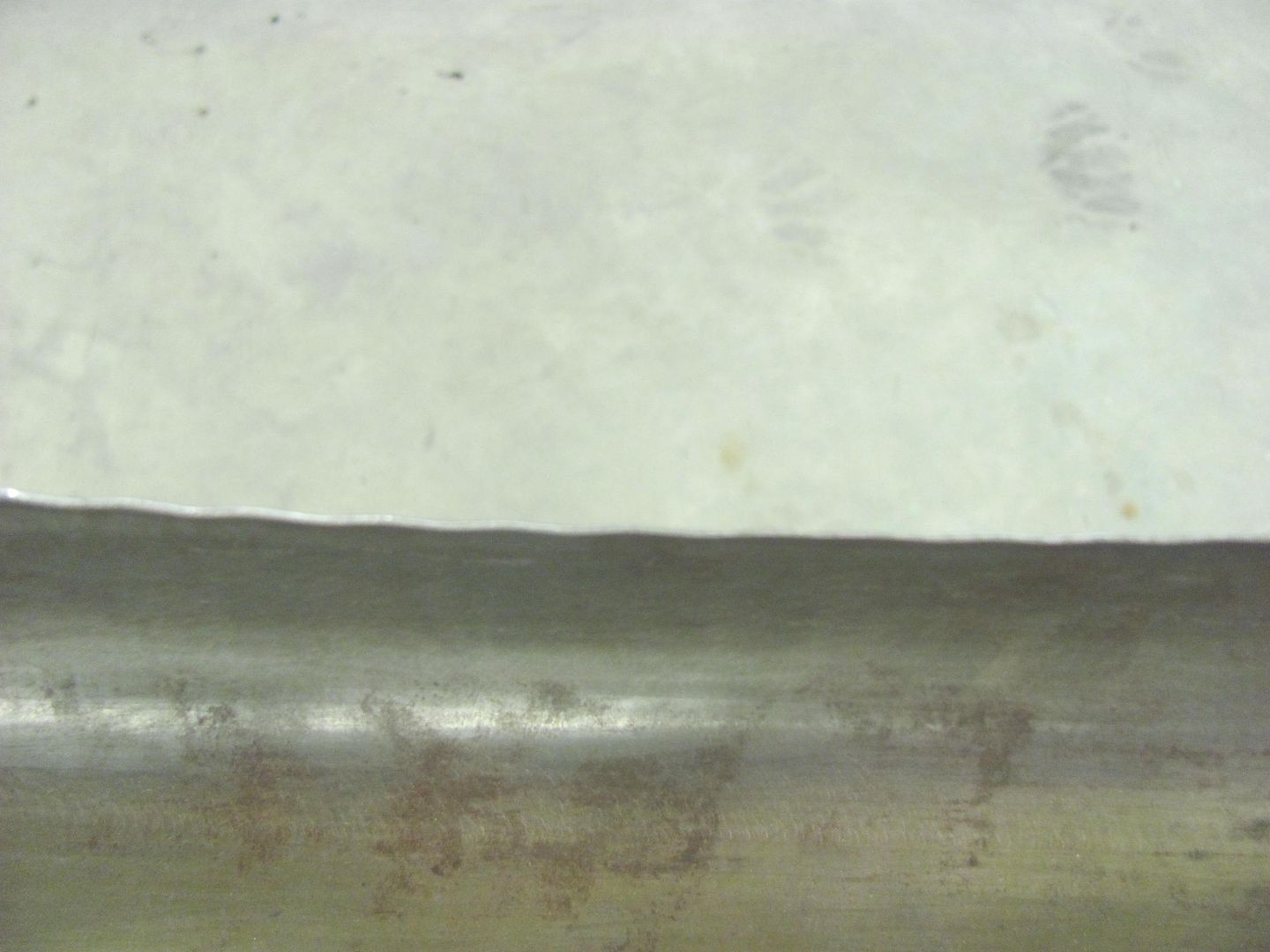
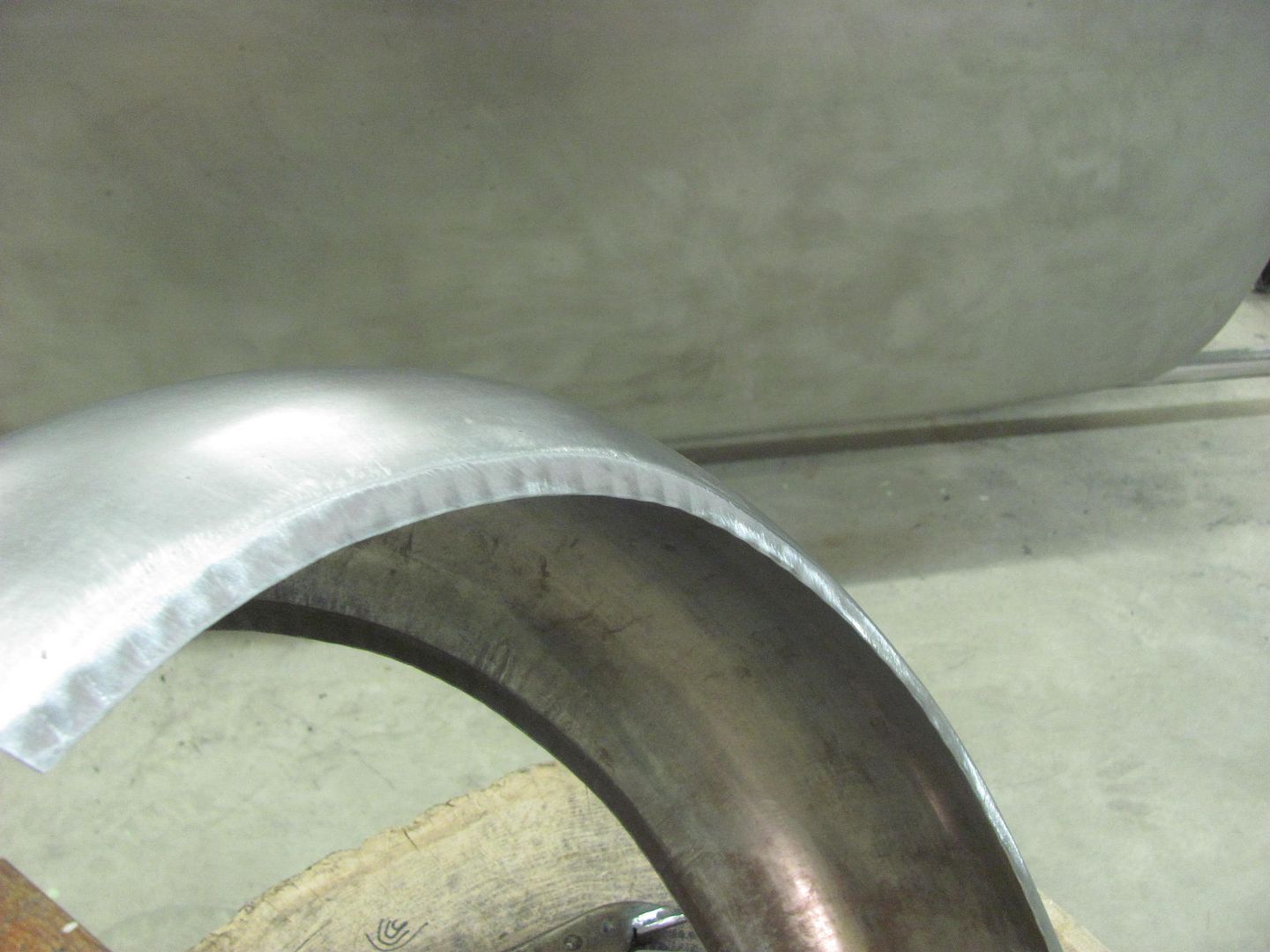
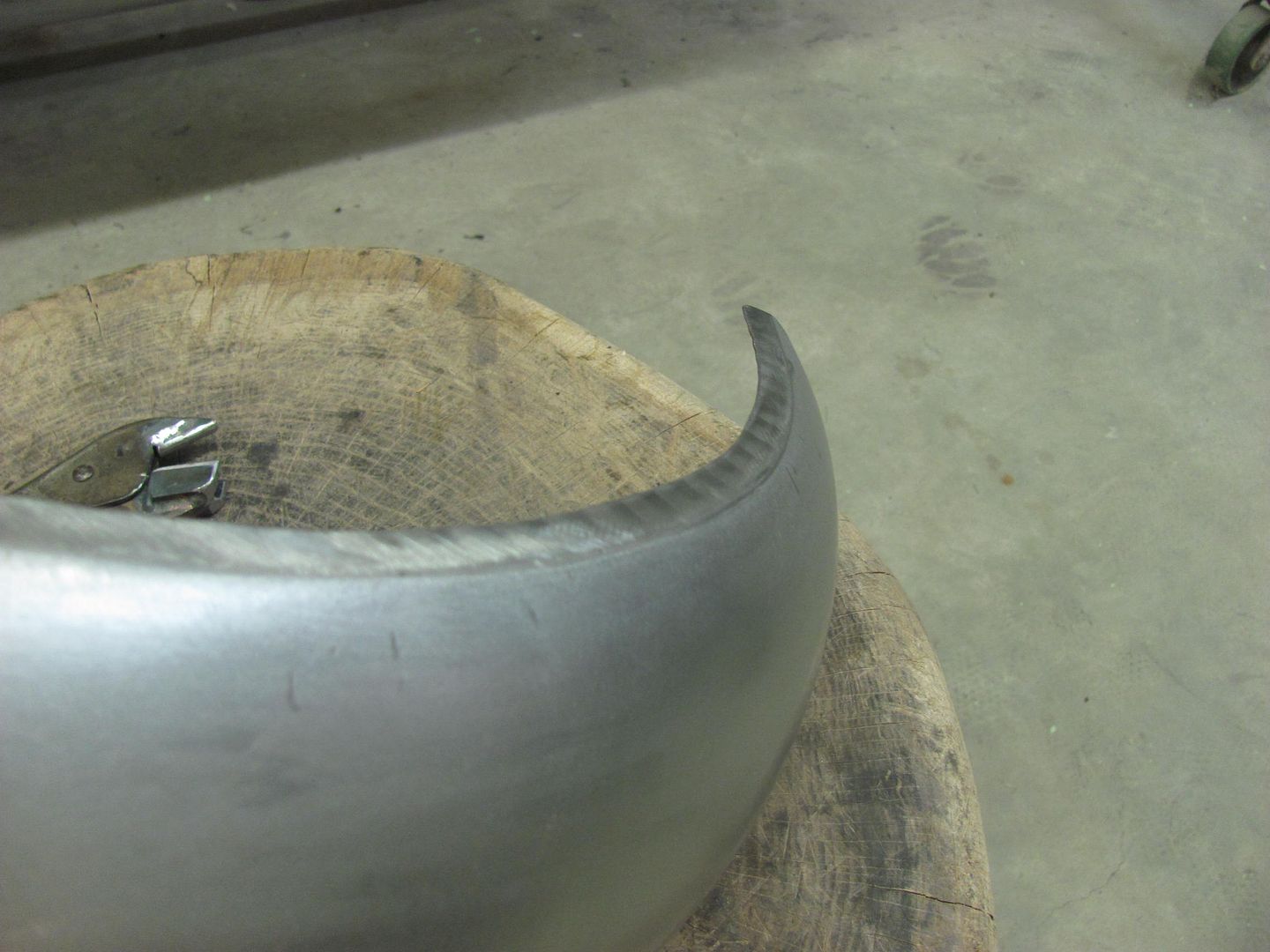
All ready for delivery!