MP&C
Member
Well after block sanding the latest coat of epoxy....
We had a local car show we could attend, but didn't know whether to take the body or the frame...
I didn't think the rotisserie would fit in my 16' trailer for some reason, but another measurement proved otherwise. Since it showed more of our metal fabrication, we opted for the body.. All loaded up, height limitations on the ceiling do require inverted travel...
At the show with the "trailer queen"
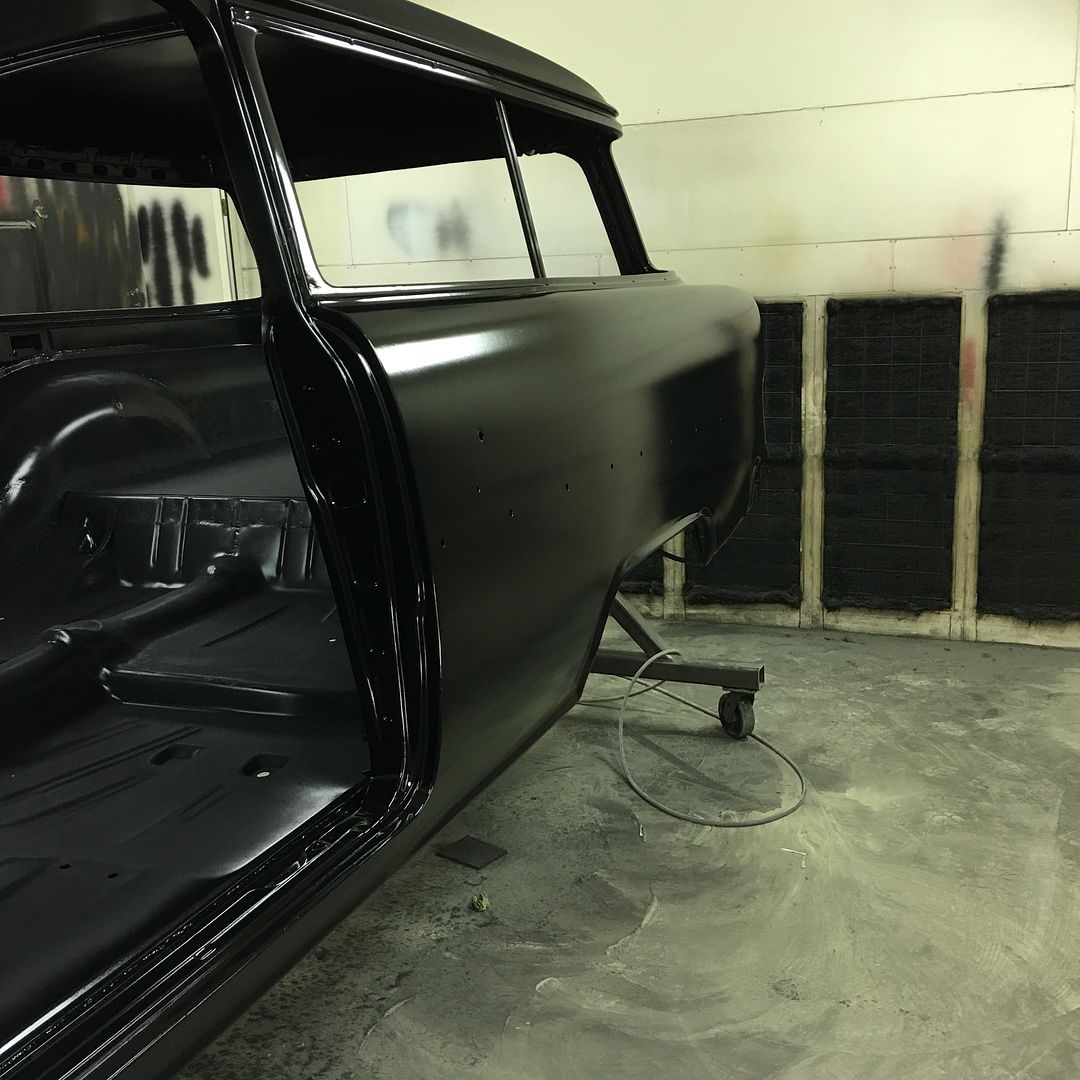
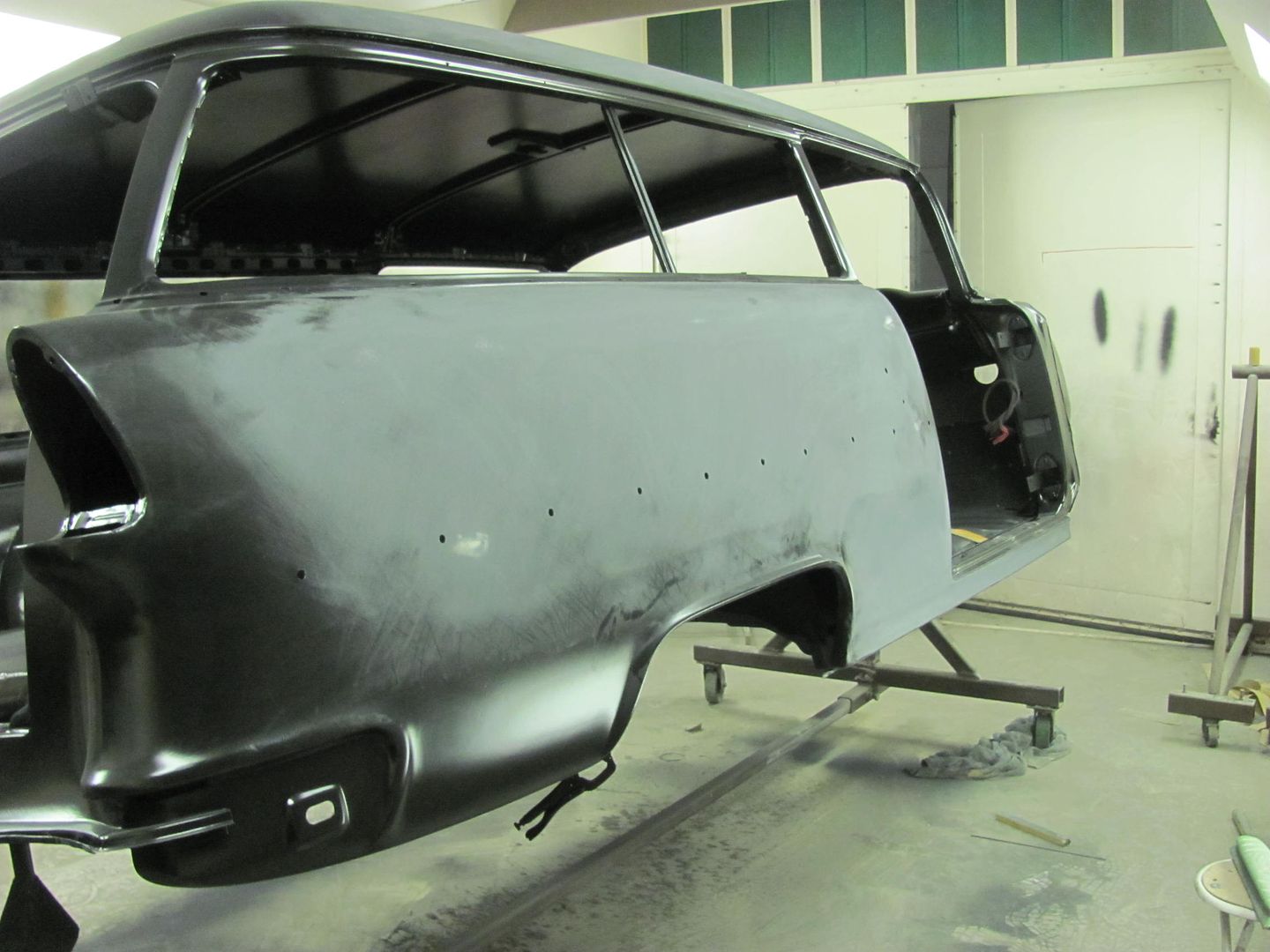
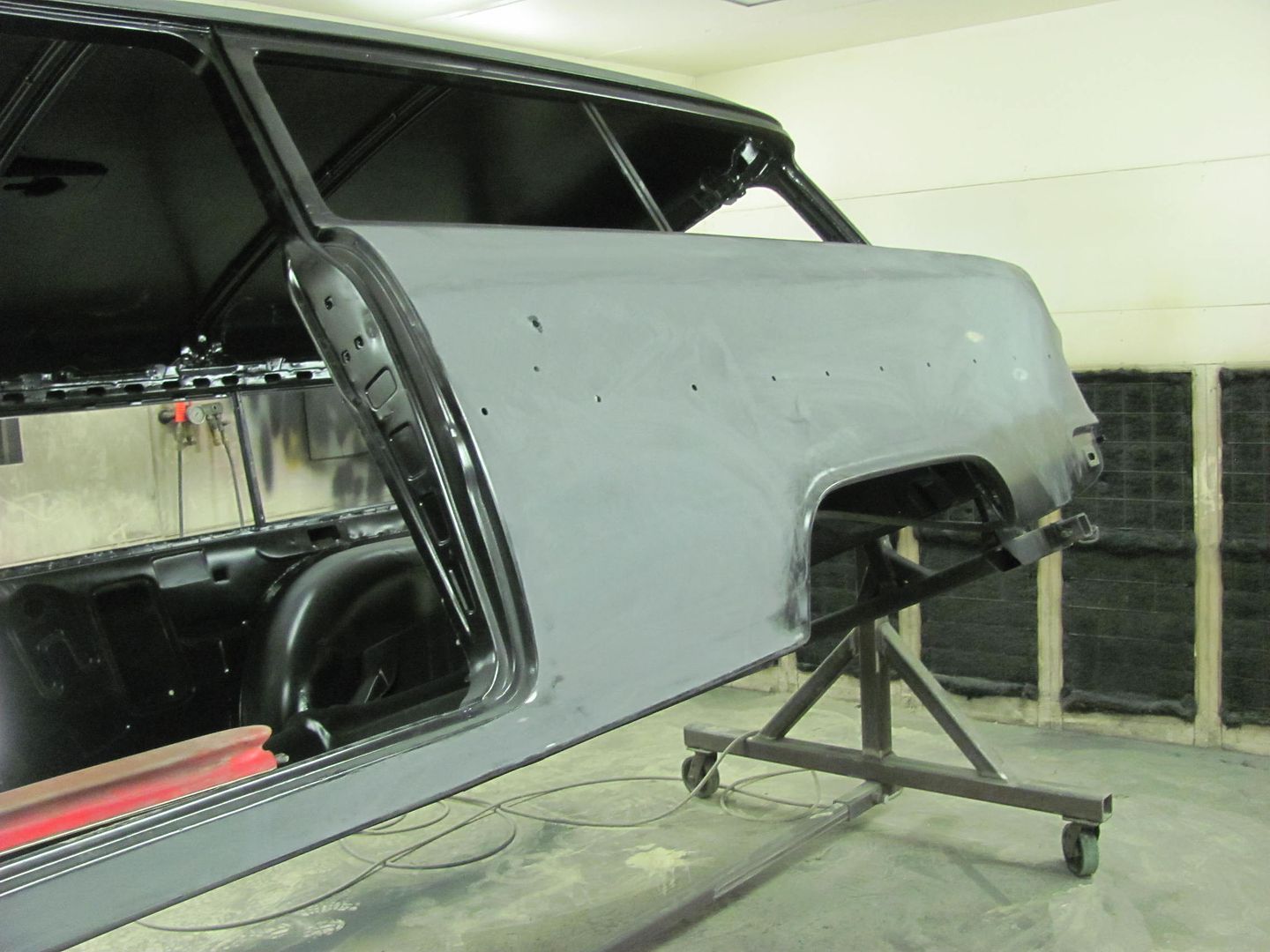
We had a local car show we could attend, but didn't know whether to take the body or the frame...
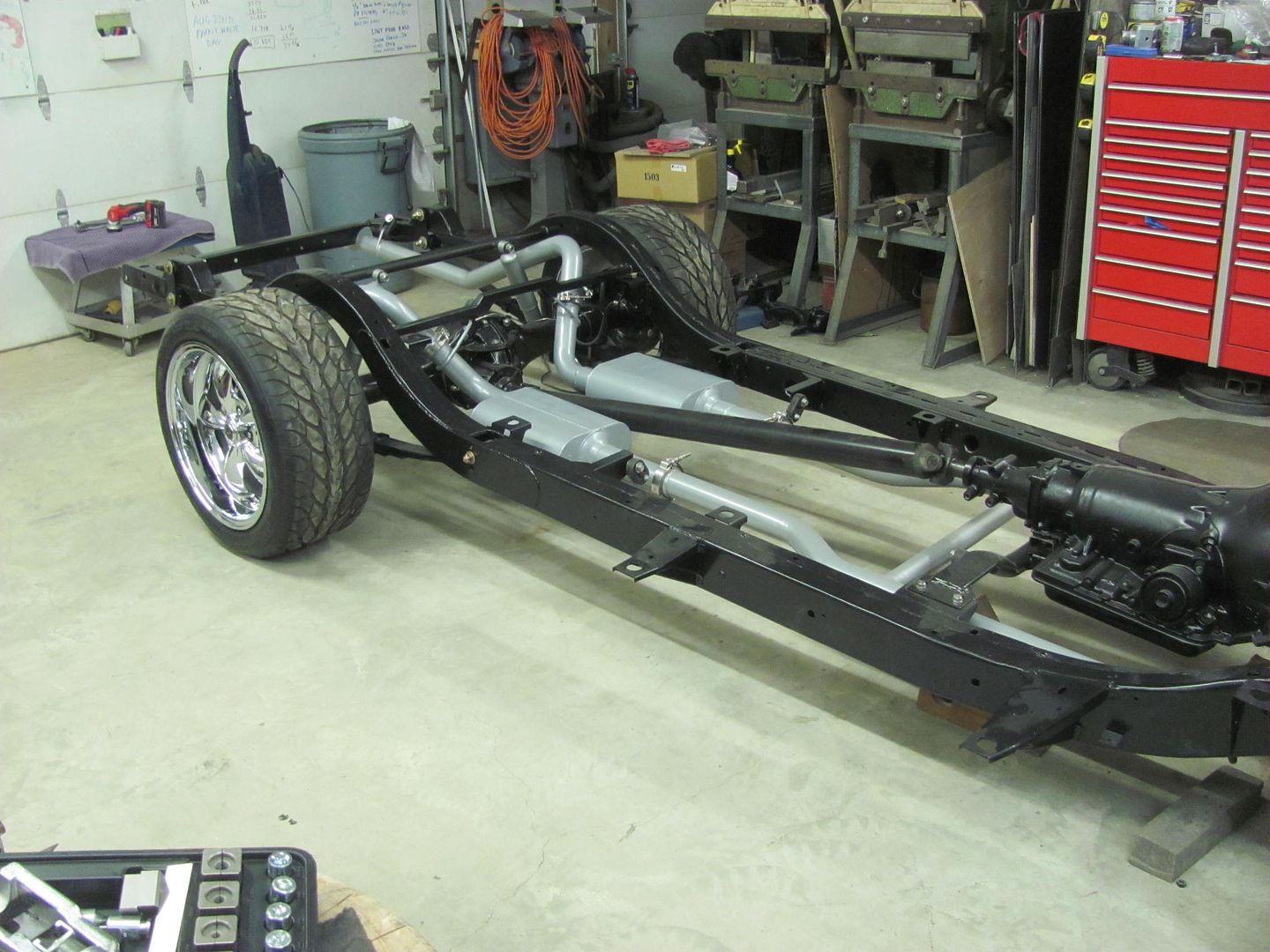
I didn't think the rotisserie would fit in my 16' trailer for some reason, but another measurement proved otherwise. Since it showed more of our metal fabrication, we opted for the body.. All loaded up, height limitations on the ceiling do require inverted travel...
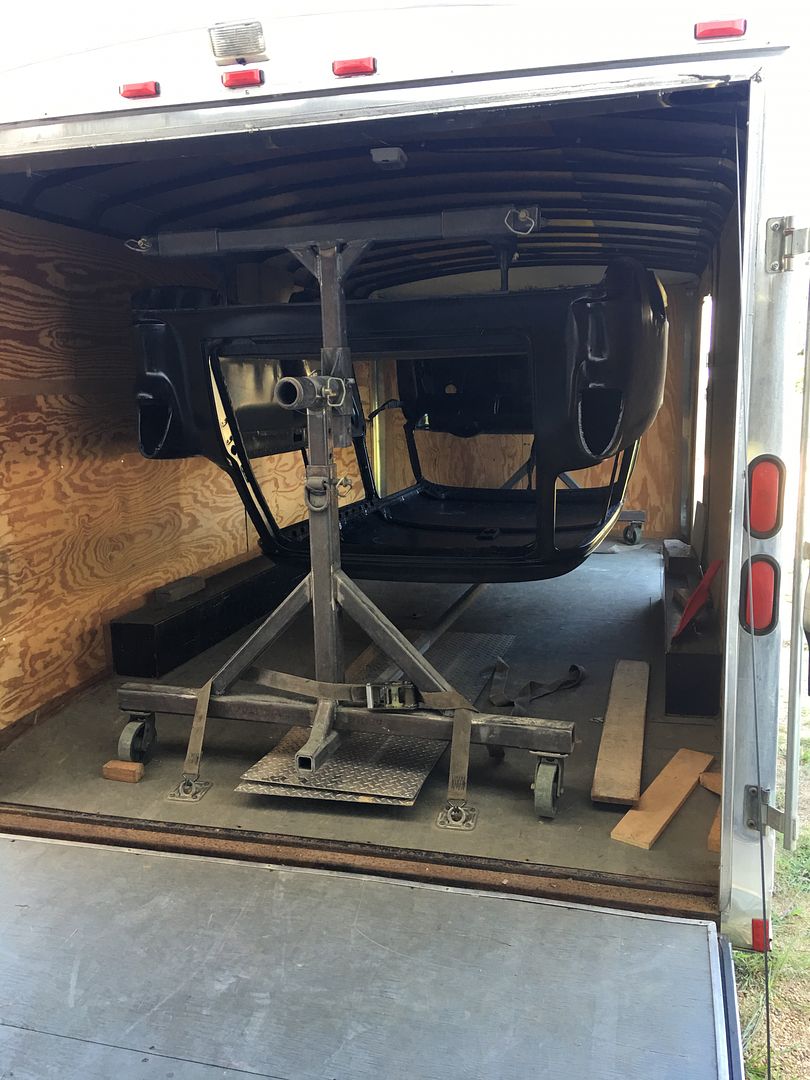
At the show with the "trailer queen"
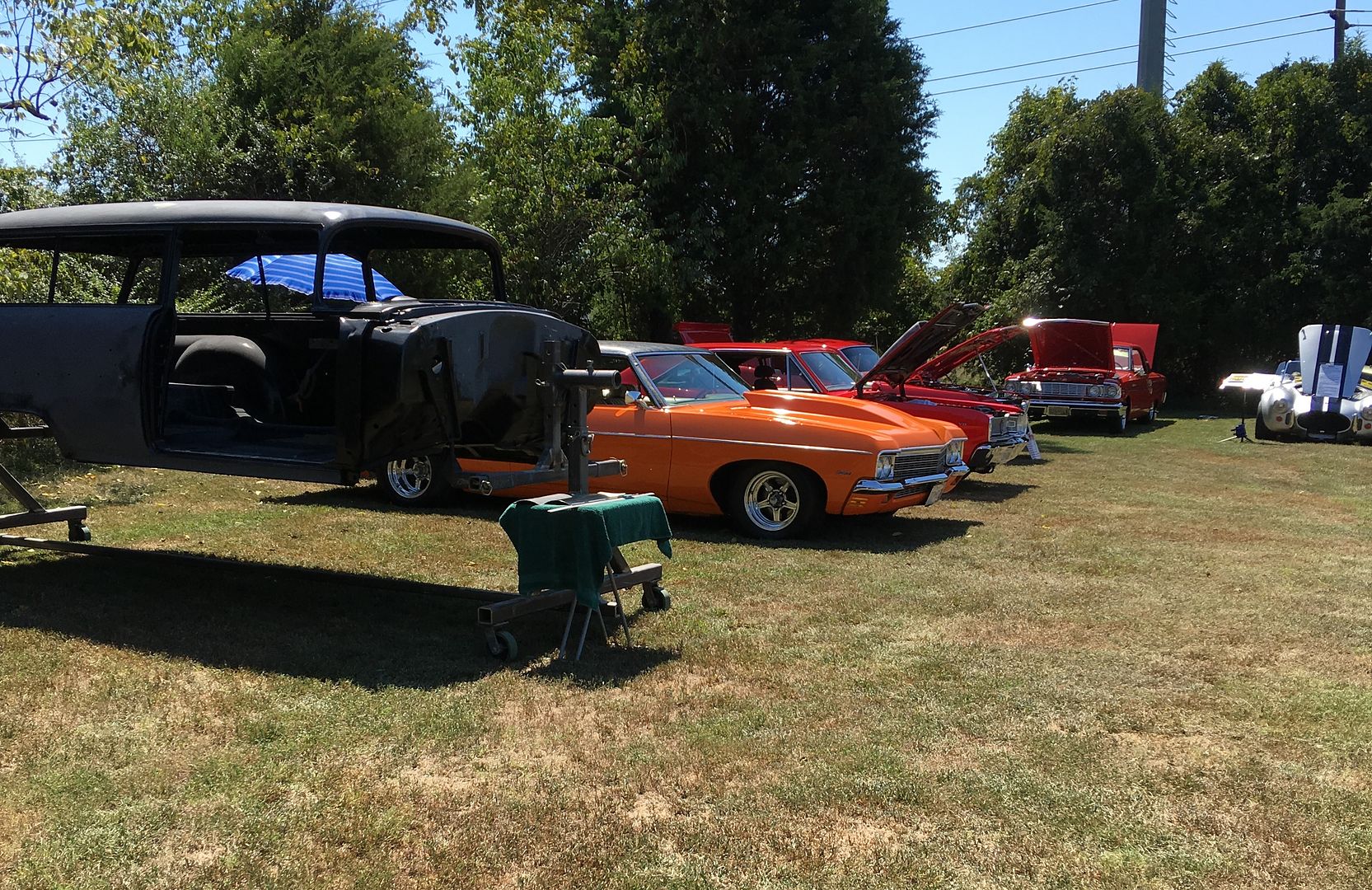