rusty428cj
Rusty Gillis
The A pillar was damaged in the accident and that is when we found the rust
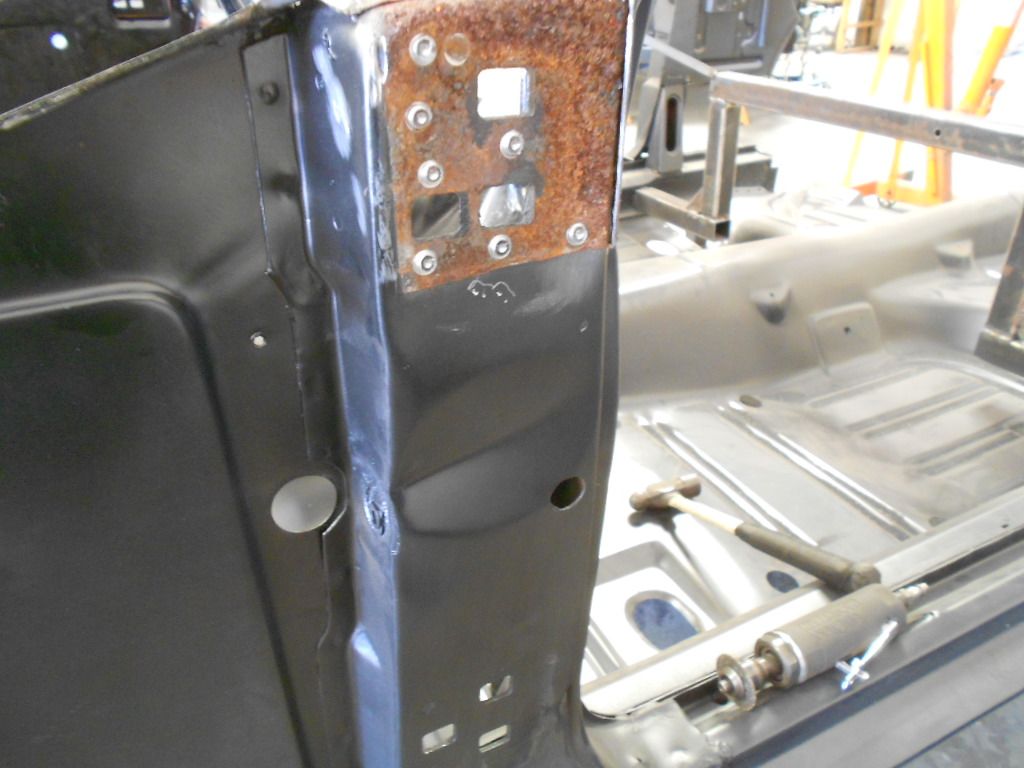
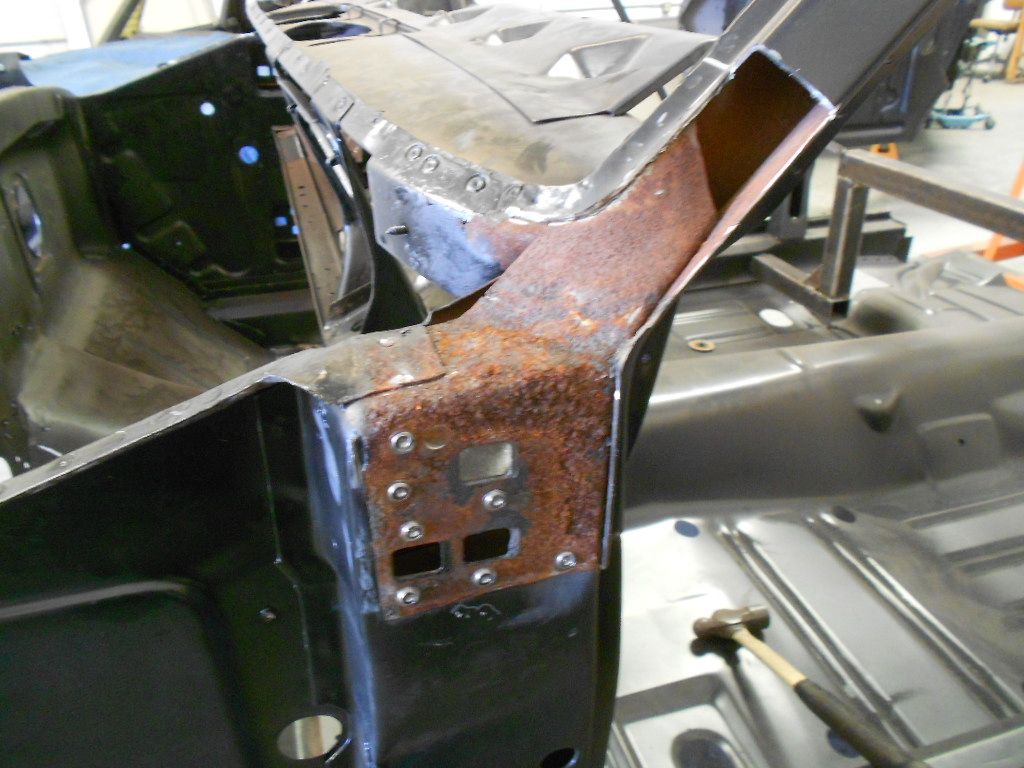
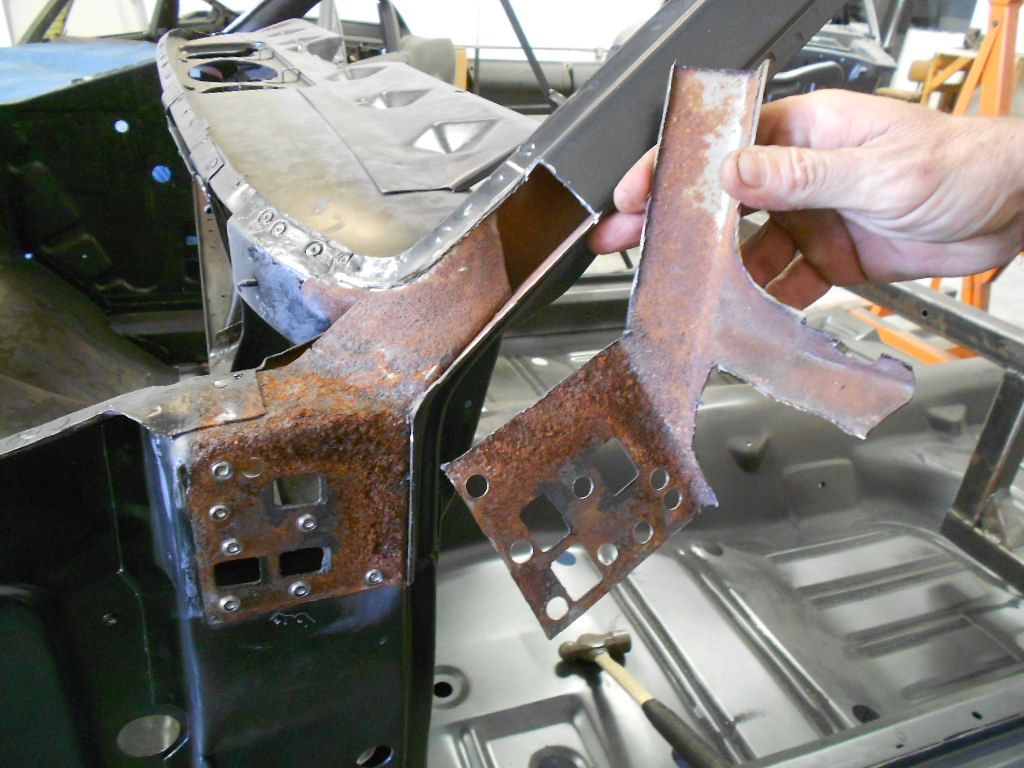
We used the other 1966 convertible we are restoring to make the jig needed for this project.
Test fitting the rear frame rails
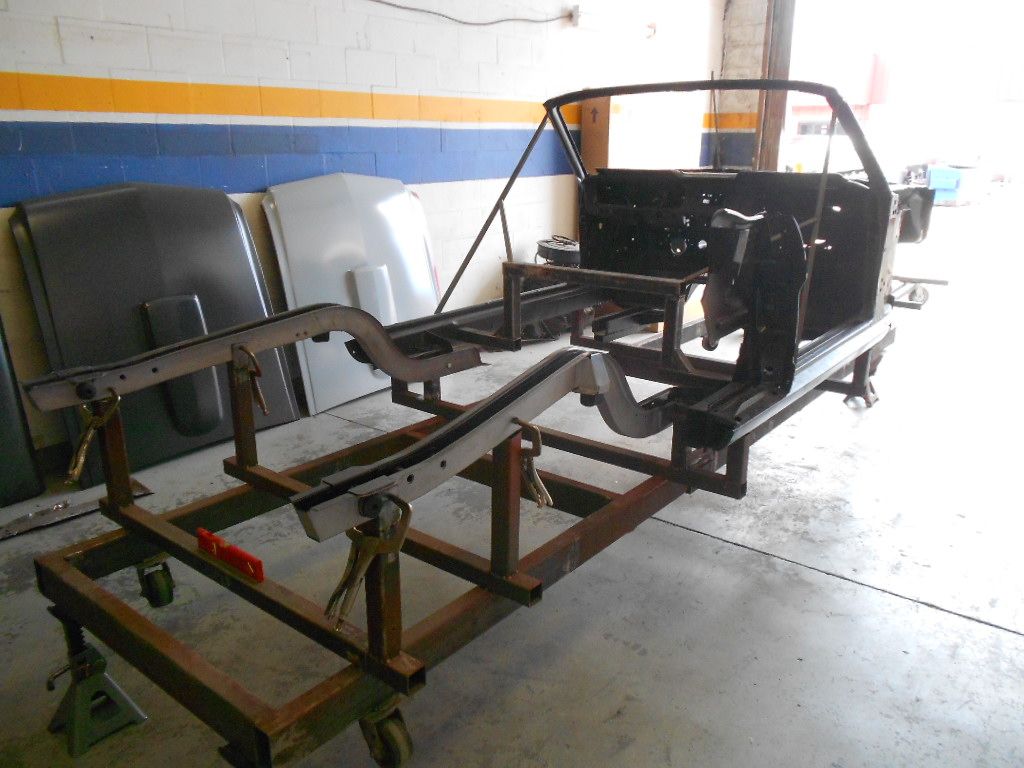
Fitting the trunk floor pan

Fitting the floor pan

The frame rails have been welded but everything else is just screwed together at this point.
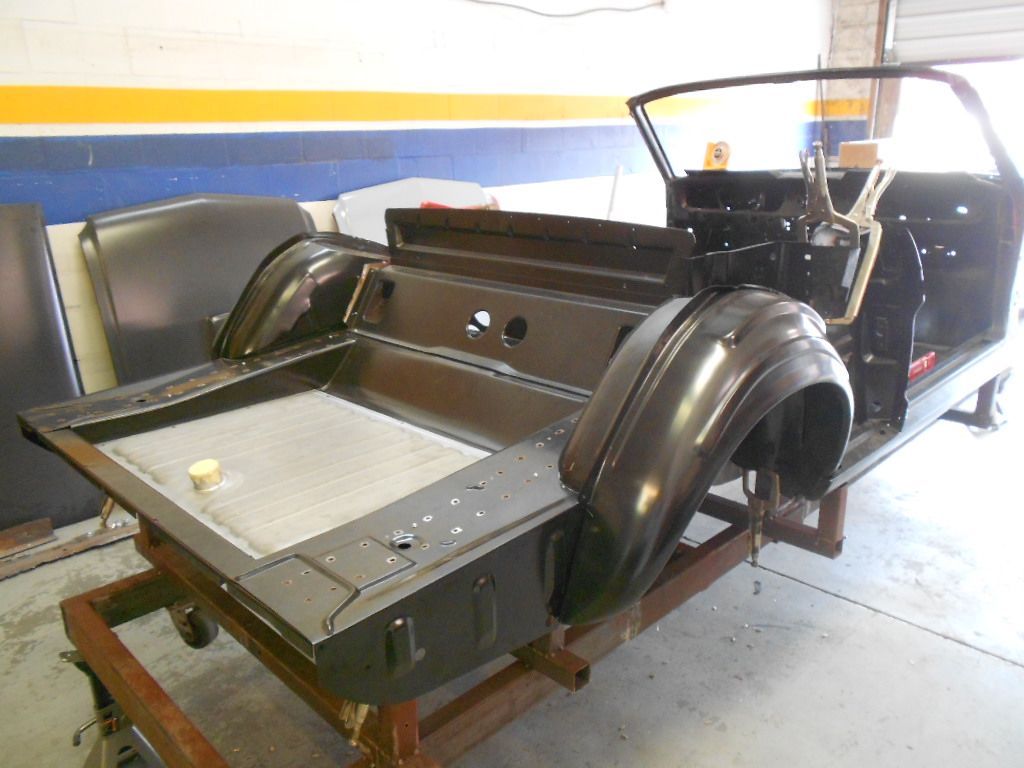
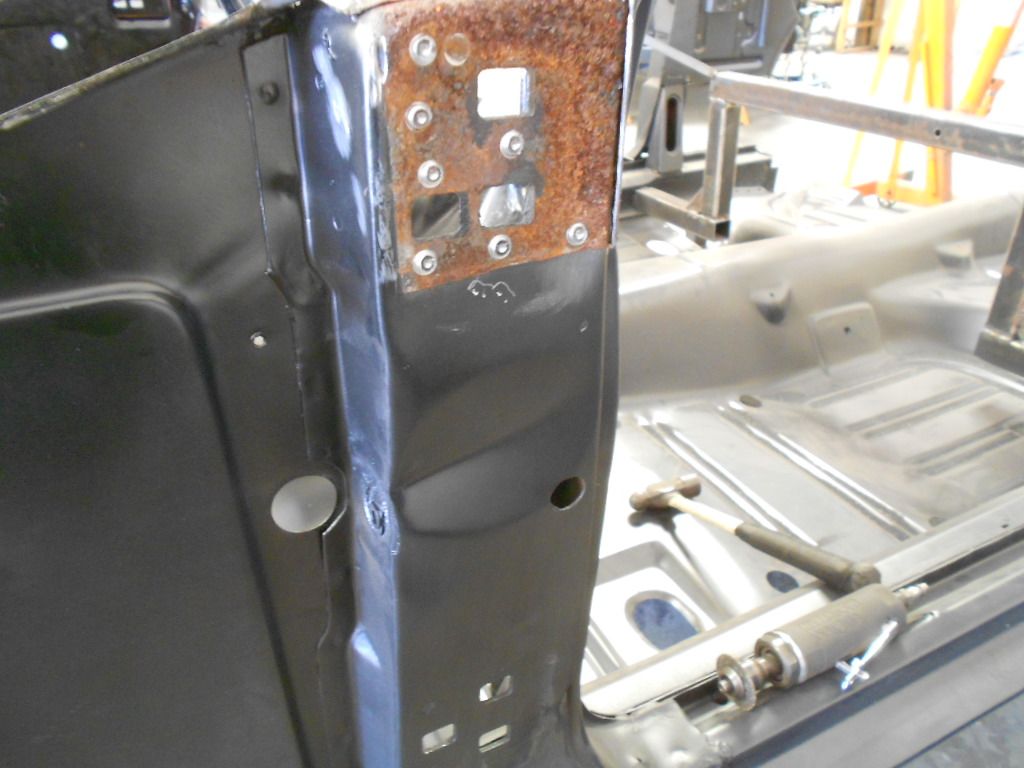
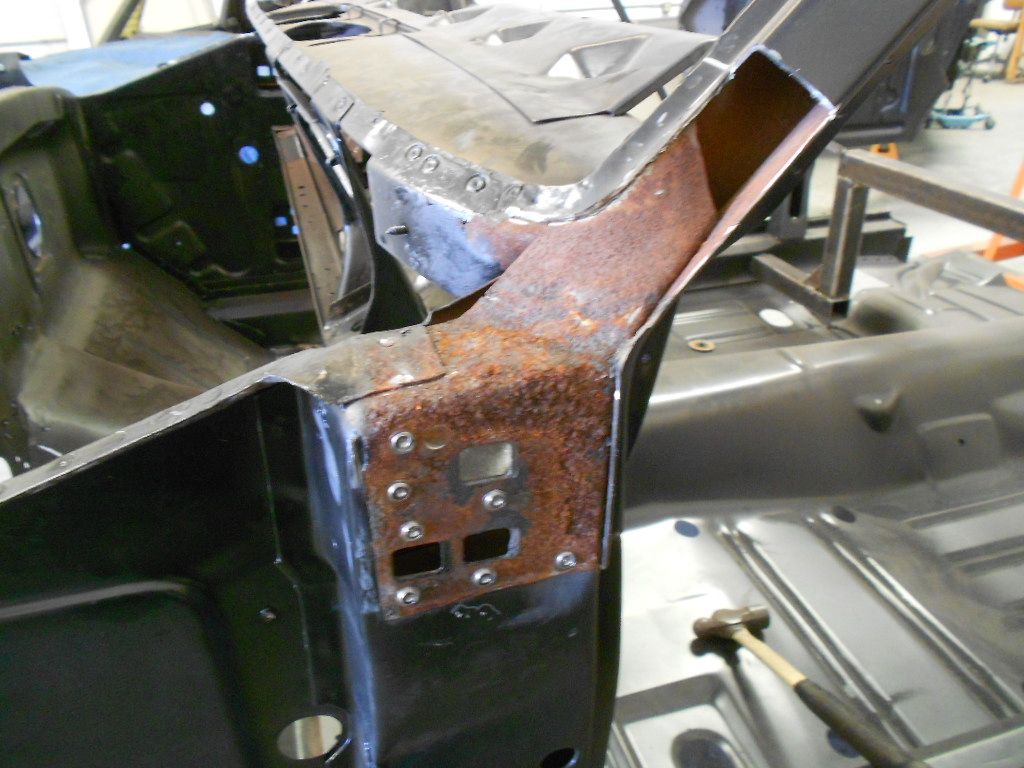
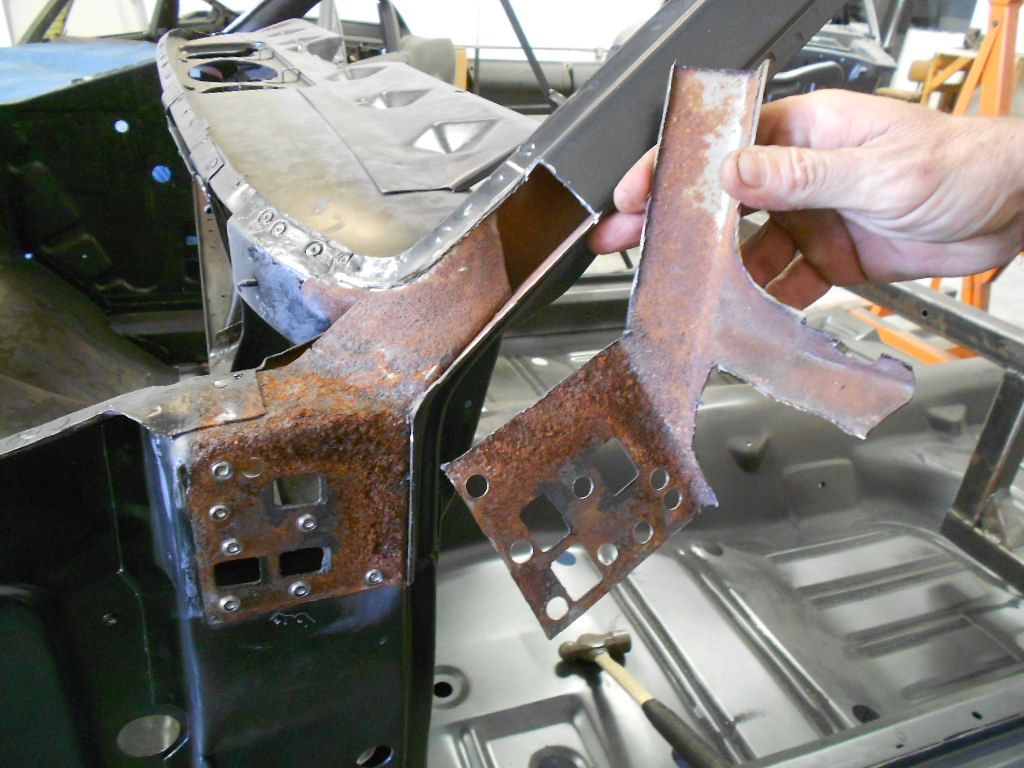
We used the other 1966 convertible we are restoring to make the jig needed for this project.
Test fitting the rear frame rails
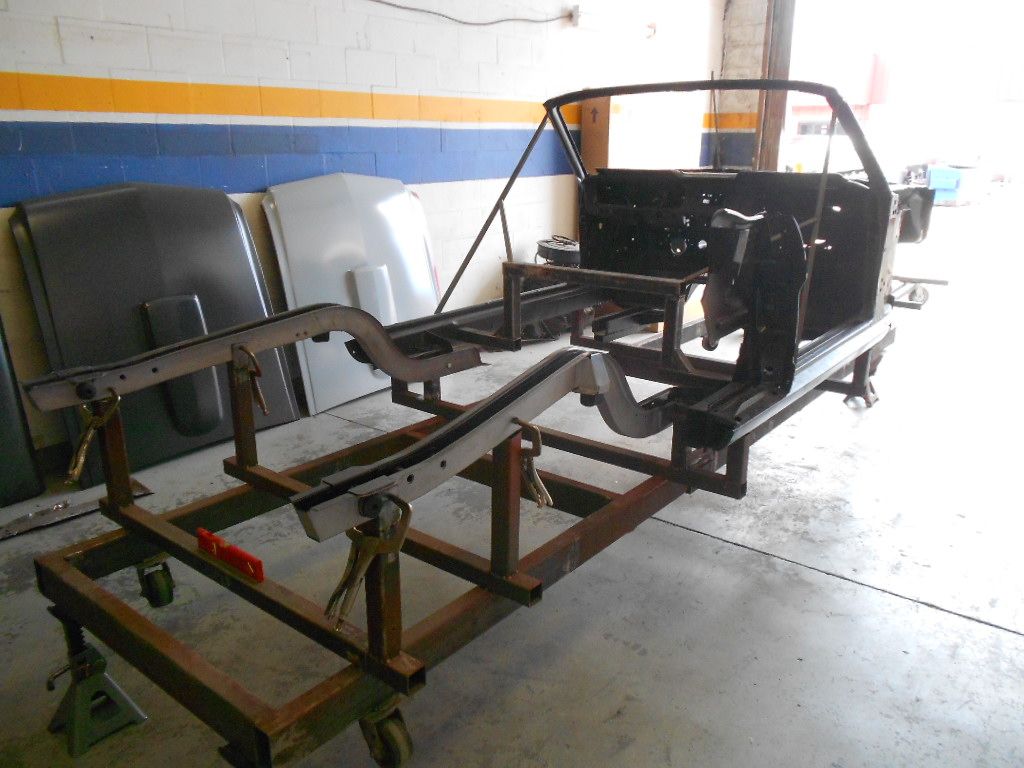
Fitting the trunk floor pan

Fitting the floor pan

The frame rails have been welded but everything else is just screwed together at this point.
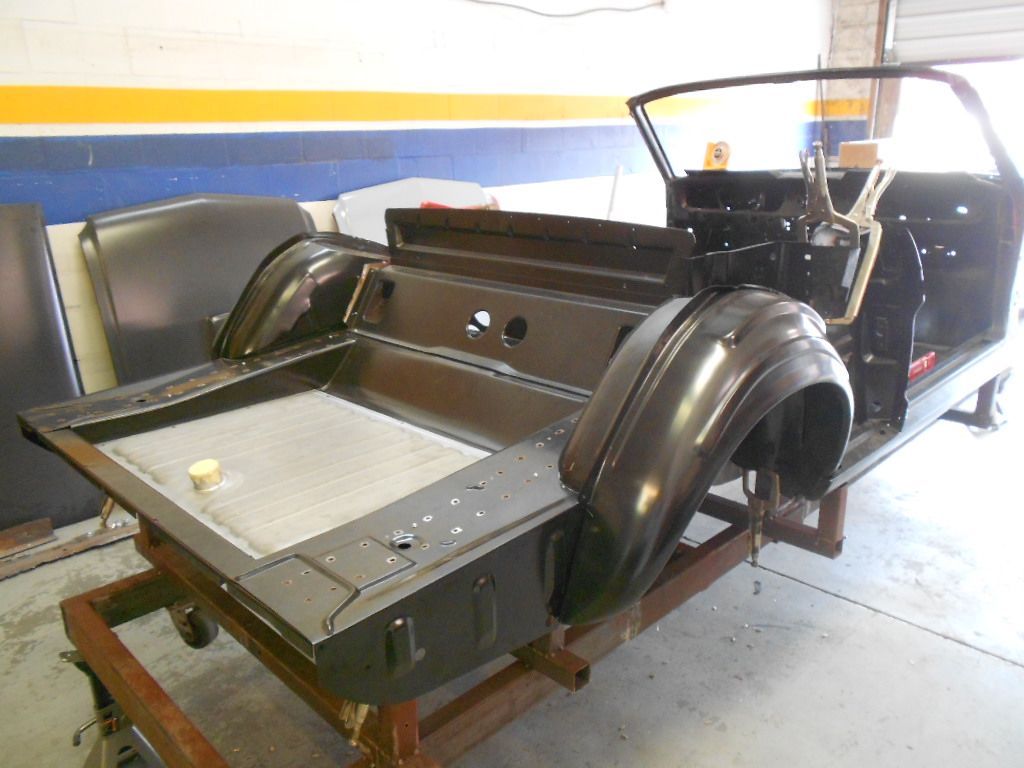