Bob Heine
Oldtimer
My 1972 Corvette (also my avatar) is my automotive guinea pig. I bought the car in 1978 and drove it for about six years.
An oil filter failure led to a complete rebuild of the 454 and it was joined by a TCI turbo 400 Street Fighter transmission.
Once the car was back on the road, the paint job really started to get to me. It included some heavy coats of clear lacquer that was starting to craze and weekly buffing wasn't helping. I stripped the car down to bare fiberglass. Before giving it a couple of coats of RM lacquer primer, I replaced the 3-piece front grille with a single aluminum bar grille that Eckler's Corvette carried for one of its custom front ends.
Once the eggcrate front grille was gone, I decided to hack up the side grilles and make them straight bar grilles as well.
At an Eckler's open house I scored a mistake -- a long L88 hood that had the wrong mounting plates glassed in. A set of unilug 16-inch Cragar mags got added when it looked like a couple of quick coats of black lacquer would put the car back on the road.
The rear bumpers had a bad case of acne. A friend gave me an equally ugly set of bumpers and decided to make a custom set from the two. Friend of a friend welded the pieces I cut back together. A few hours with hand files leveled the welds.
Because chrome plating was expensive back in the mid-80s I decided not to spend the $60 and just painted them black. Hey, the monochromatic look was gaining popularity.
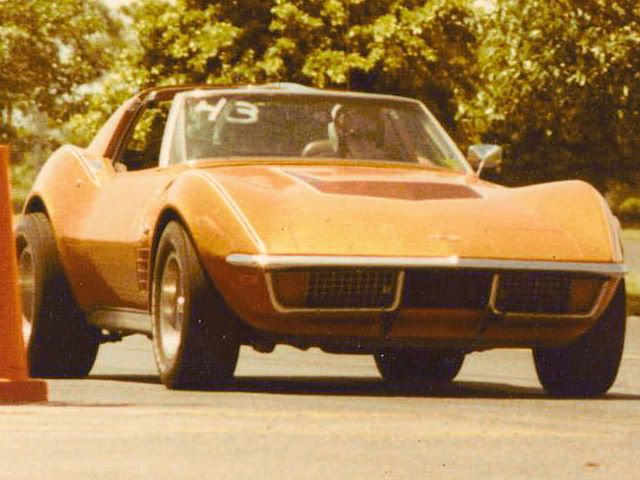
An oil filter failure led to a complete rebuild of the 454 and it was joined by a TCI turbo 400 Street Fighter transmission.
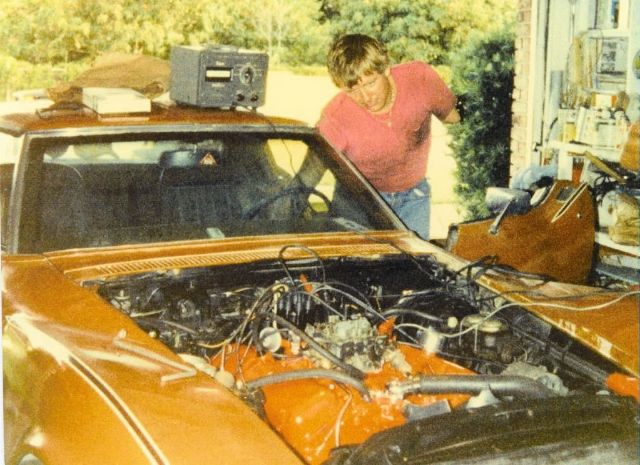
Once the car was back on the road, the paint job really started to get to me. It included some heavy coats of clear lacquer that was starting to craze and weekly buffing wasn't helping. I stripped the car down to bare fiberglass. Before giving it a couple of coats of RM lacquer primer, I replaced the 3-piece front grille with a single aluminum bar grille that Eckler's Corvette carried for one of its custom front ends.
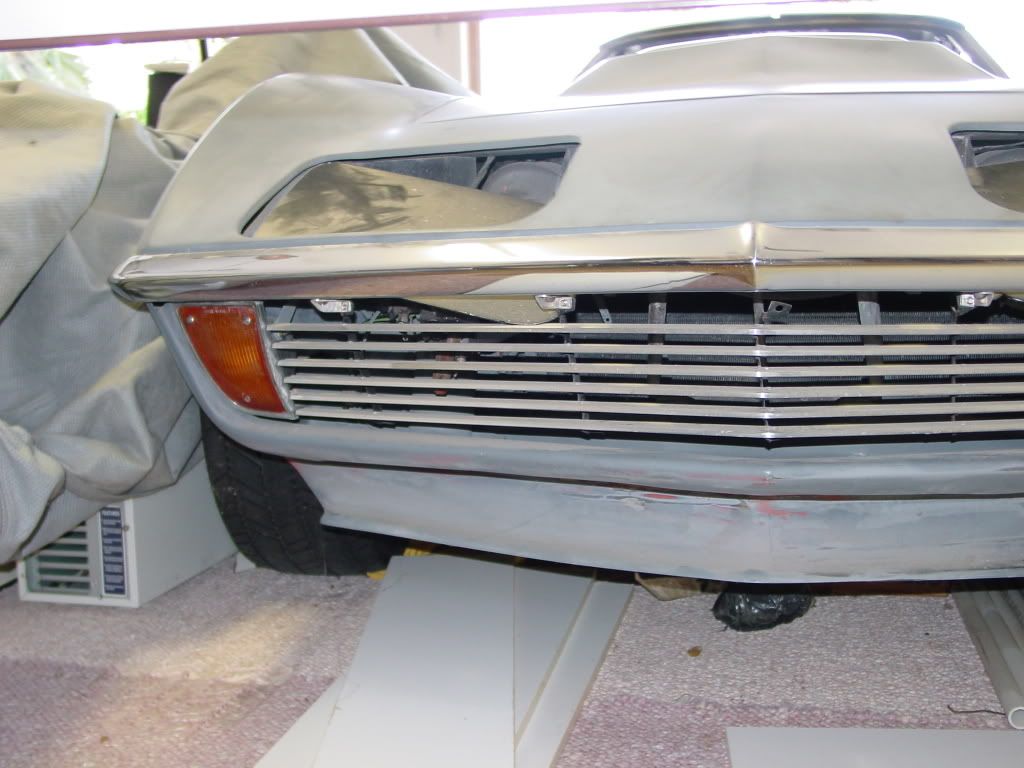
Once the eggcrate front grille was gone, I decided to hack up the side grilles and make them straight bar grilles as well.
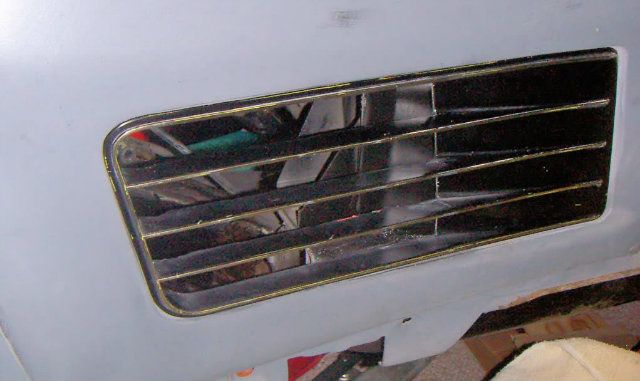
At an Eckler's open house I scored a mistake -- a long L88 hood that had the wrong mounting plates glassed in. A set of unilug 16-inch Cragar mags got added when it looked like a couple of quick coats of black lacquer would put the car back on the road.
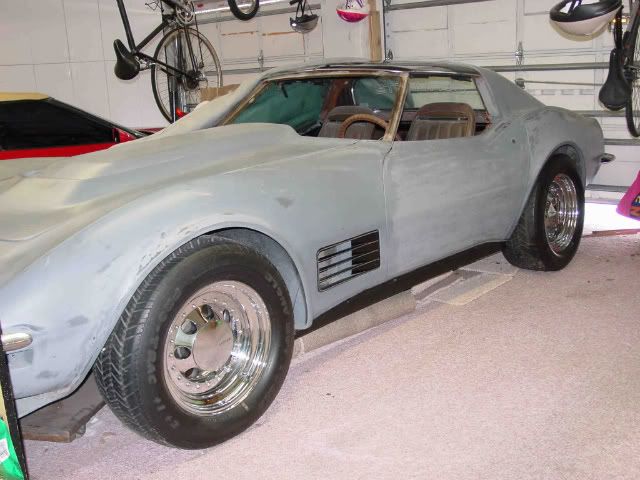
The rear bumpers had a bad case of acne. A friend gave me an equally ugly set of bumpers and decided to make a custom set from the two. Friend of a friend welded the pieces I cut back together. A few hours with hand files leveled the welds.
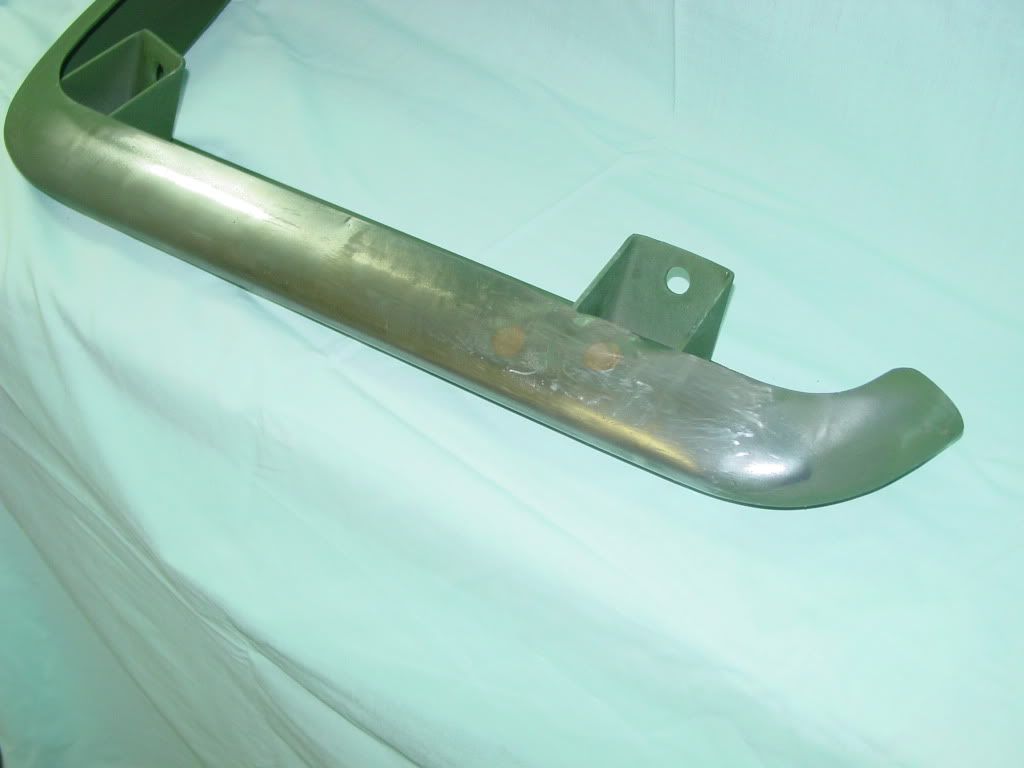
Because chrome plating was expensive back in the mid-80s I decided not to spend the $60 and just painted them black. Hey, the monochromatic look was gaining popularity.
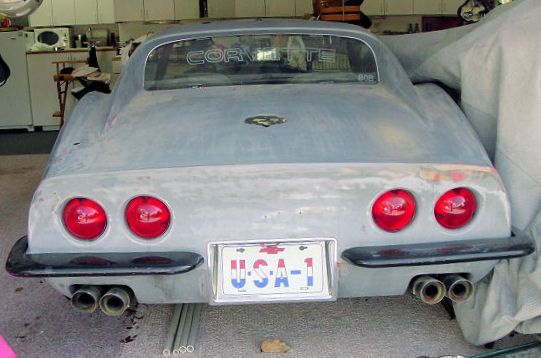