rustover
Member
This may be a stupid question, but I thought I would get some advice before I proceed. I'm replacing the deck filler panel on my 72 Camaro, and I have the panel test fitted and in the same location as the original. At first glance I notice they short changed me some metal on the flange that welds to the trunk gutters for the weather stripping . Here are a few pics of what I'm talking about.
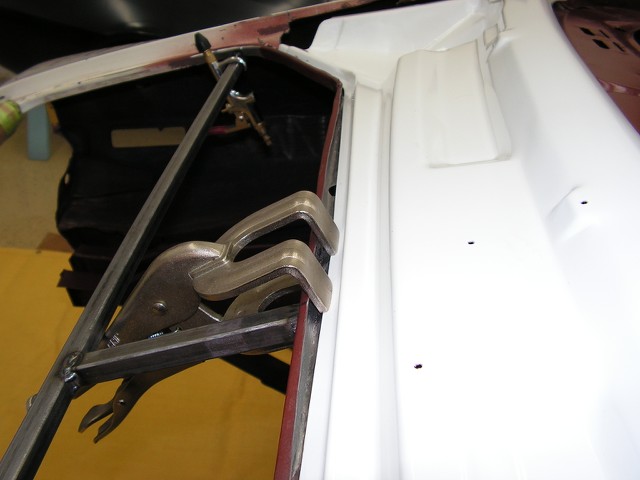

To me it looks worse in person than in the pics. I was planning on plug welding this area with 1/4 inch holes. I don't have enough metal for 1/4 inch, I could maybe do a 3/16. I was also thinking about just doing some stitch welding in this area. I guess I could get creative and butt weld some metal and then do the 1/4 inch holes.
Anyway just wanted to ask what would be the best method.
Thanks for the help,
Russ
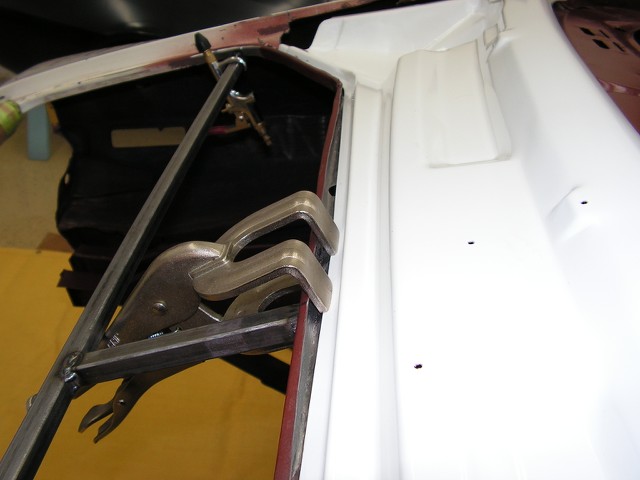

To me it looks worse in person than in the pics. I was planning on plug welding this area with 1/4 inch holes. I don't have enough metal for 1/4 inch, I could maybe do a 3/16. I was also thinking about just doing some stitch welding in this area. I guess I could get creative and butt weld some metal and then do the 1/4 inch holes.
Anyway just wanted to ask what would be the best method.
Thanks for the help,
Russ