rustover
Member
Hey guys, I'm in the process of replacing my trunk pan in my 72 Camaro. I have the whole pan fitted to the car. Its where it is going be and there really isn't any movement to it. Its non adjustable at this point. I have check and double checked and best I can tell I have it right. I have also test fitted the tail panel and its close.
I didn't remove the whole pan. I left the shock tower area in the car. Reason being I didn't want to try to separate all that metal. In this area there is the trunk pan, inner wheel house and a frame brace and a shock tower inner brace. So I opted to make a splice in that area. I now have the trunk fitted in that area with about an inch overlap.
Here is where I need some solid advice. At first when I got to this point I was planning on scribing a line and doing a butt weld. Looking at how its fitting I'm a little worried that once I cut it, the original piece and the new piece wont line up flush to do a butt weld. I may be able to hammer and dolly the new metal over but I'm not sure.
Anyway, I'm wanted some advice on where to go from here. I could lap weld this area and I guess it would be a good repair, The seams are all hidden by the frame brace underneath. I will still have to push the top metal down with a driver until I get my tacks, then I could hammer the metal tight. Or I could go ahead and proceed with my scribe lines and take my time until I have the metal lined up. What do you guys think is the best route to take? Thanks, Russ
Here are some pics:


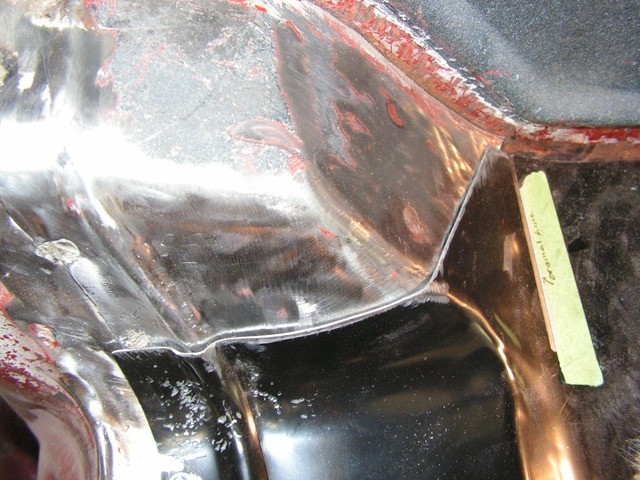
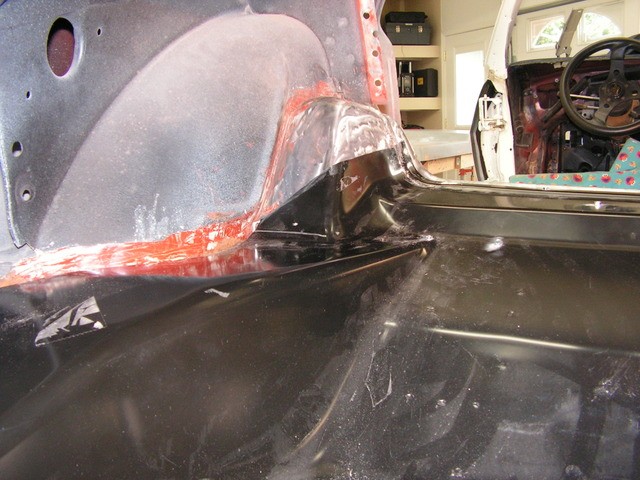
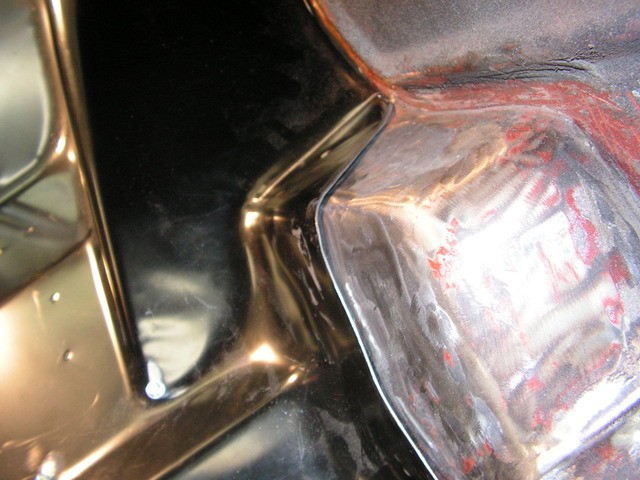
I didn't remove the whole pan. I left the shock tower area in the car. Reason being I didn't want to try to separate all that metal. In this area there is the trunk pan, inner wheel house and a frame brace and a shock tower inner brace. So I opted to make a splice in that area. I now have the trunk fitted in that area with about an inch overlap.
Here is where I need some solid advice. At first when I got to this point I was planning on scribing a line and doing a butt weld. Looking at how its fitting I'm a little worried that once I cut it, the original piece and the new piece wont line up flush to do a butt weld. I may be able to hammer and dolly the new metal over but I'm not sure.
Anyway, I'm wanted some advice on where to go from here. I could lap weld this area and I guess it would be a good repair, The seams are all hidden by the frame brace underneath. I will still have to push the top metal down with a driver until I get my tacks, then I could hammer the metal tight. Or I could go ahead and proceed with my scribe lines and take my time until I have the metal lined up. What do you guys think is the best route to take? Thanks, Russ
Here are some pics:


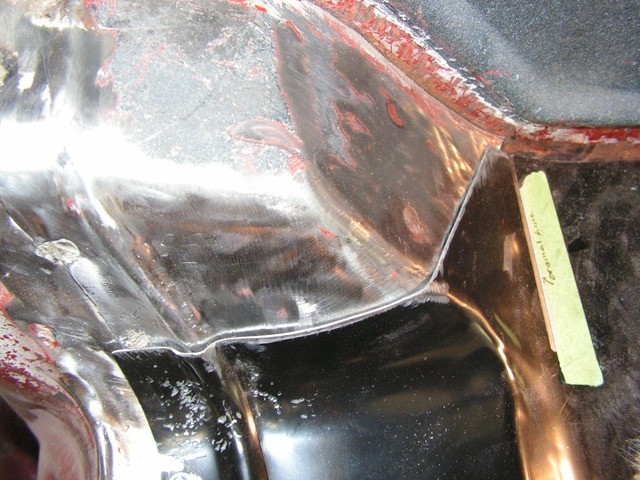
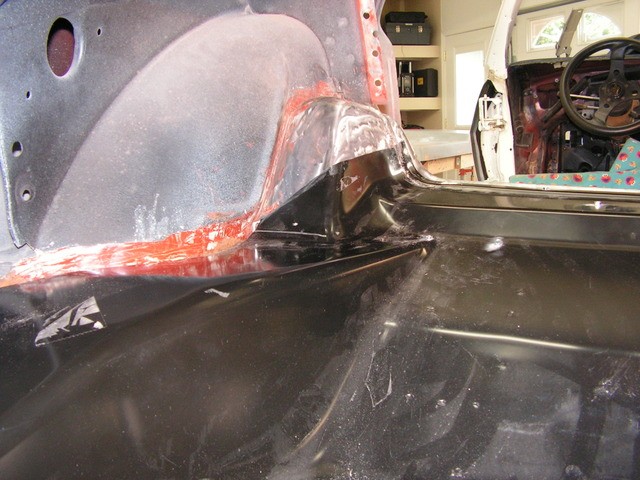
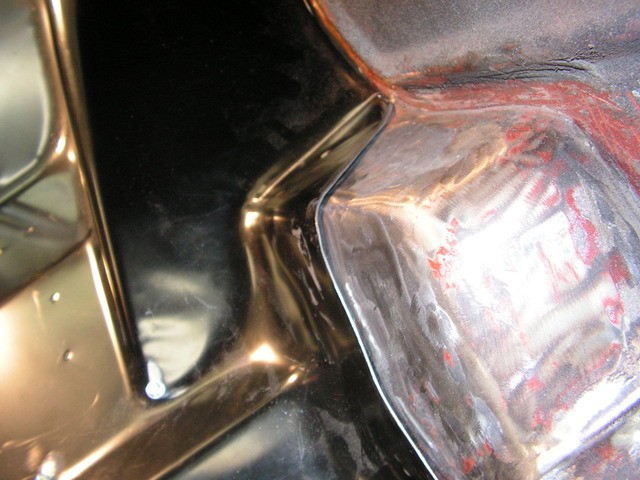