MP&C
Member
Was working today on some metal bumping on the drivers quarter, so a profile template was needed... Took a 1-1/2 x48 piece of 19 ga and used the mag brake to fold it, then the bead roller to flatten.
Then used the kick shrinker to get it to match the contour of the rear of the door, this will give us a close match to the front half of the quarter... (The hand operated shrinkers should work just as well for those with that model)
If you shrink too much, no need to change dies, just shrink the rear portion of the template (away from the body)
Ends are radiused...
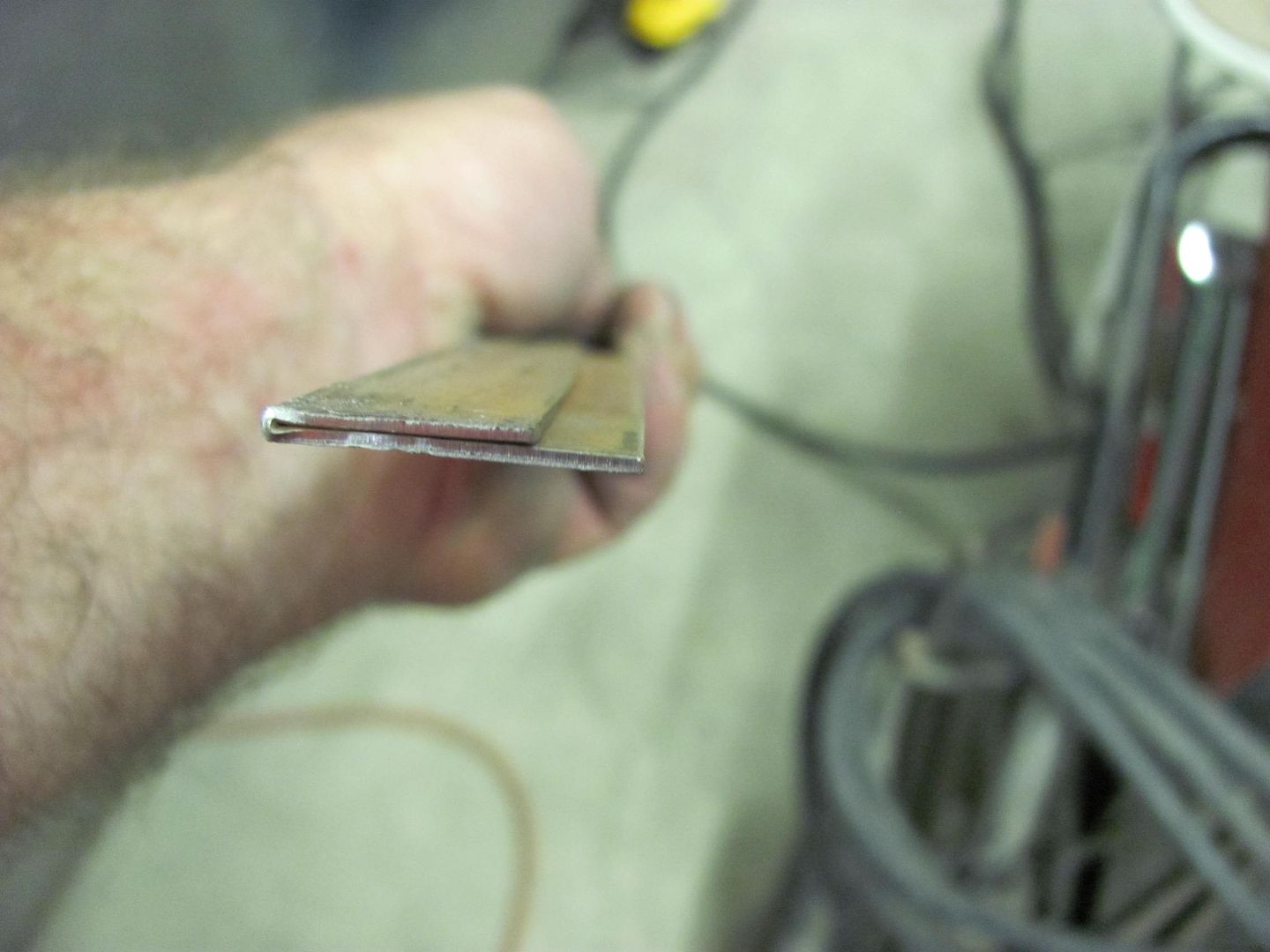
Then used the kick shrinker to get it to match the contour of the rear of the door, this will give us a close match to the front half of the quarter... (The hand operated shrinkers should work just as well for those with that model)
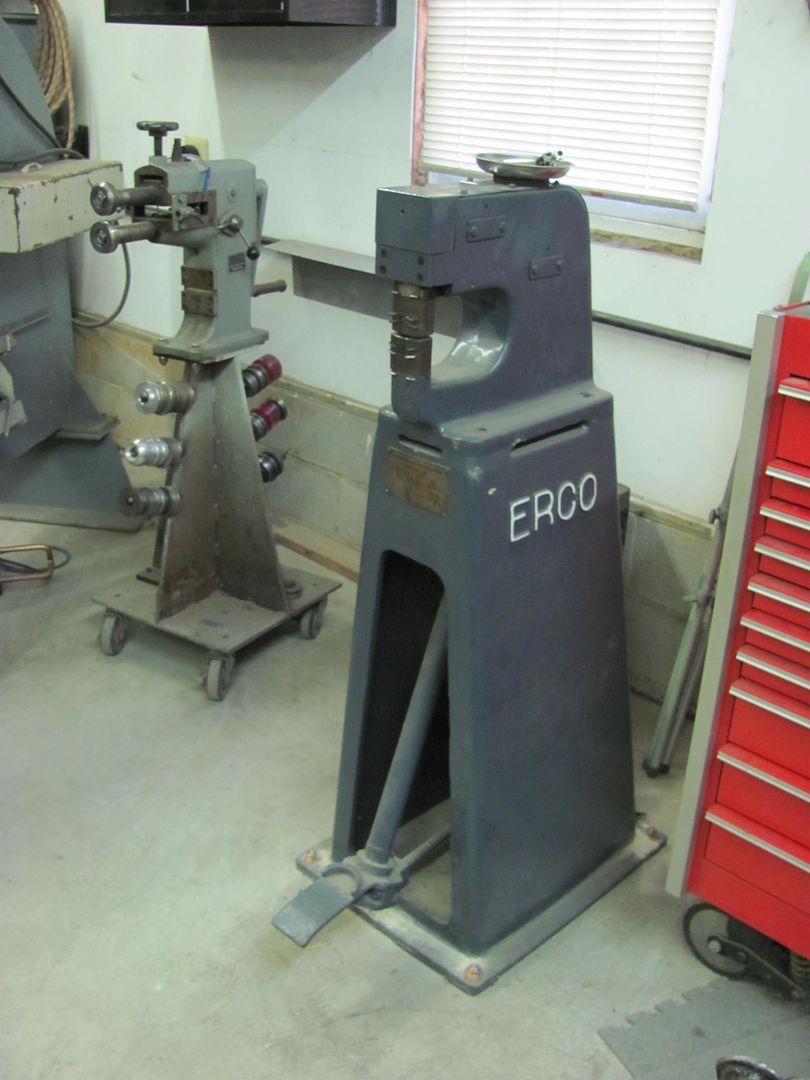
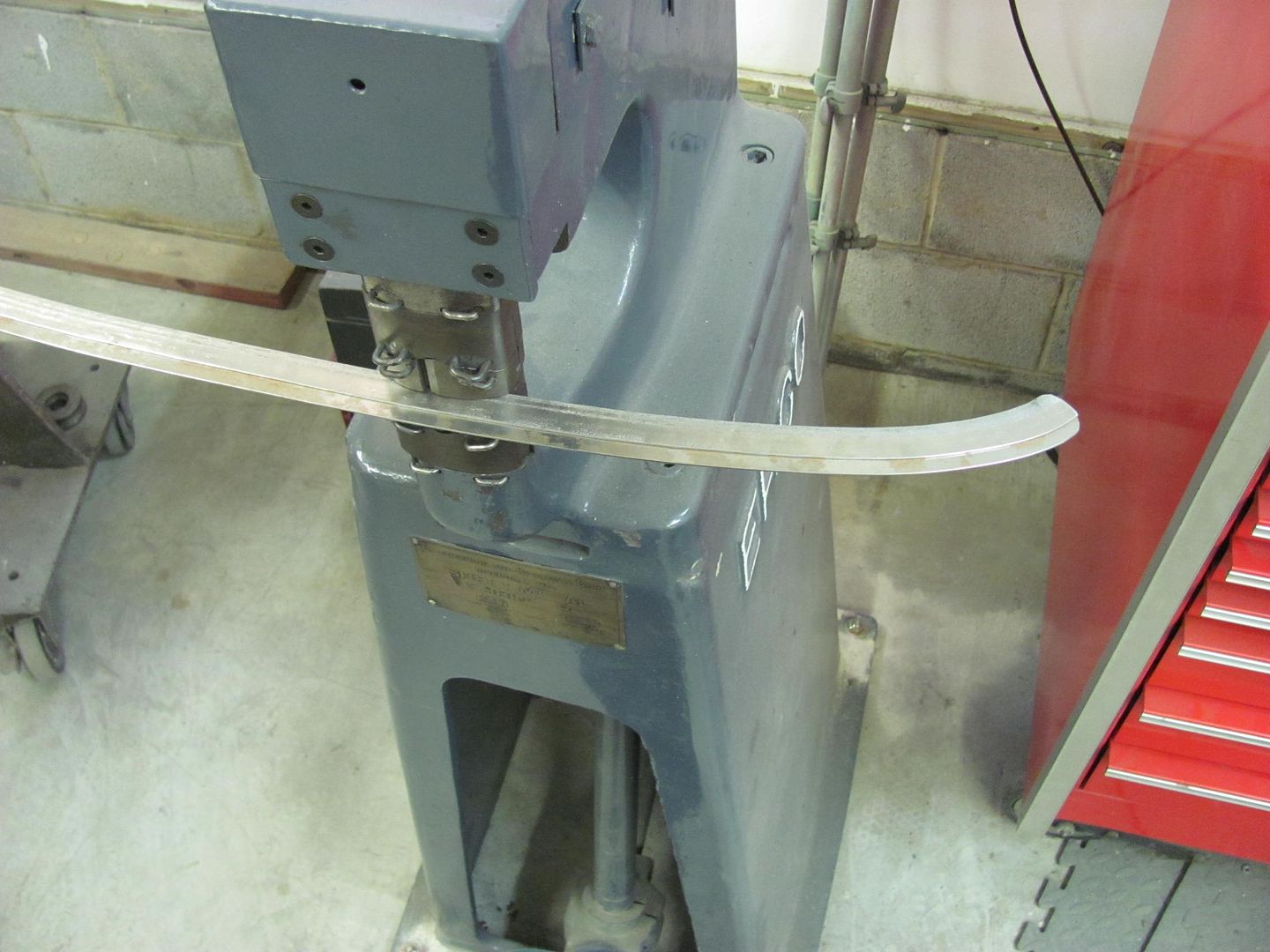
If you shrink too much, no need to change dies, just shrink the rear portion of the template (away from the body)
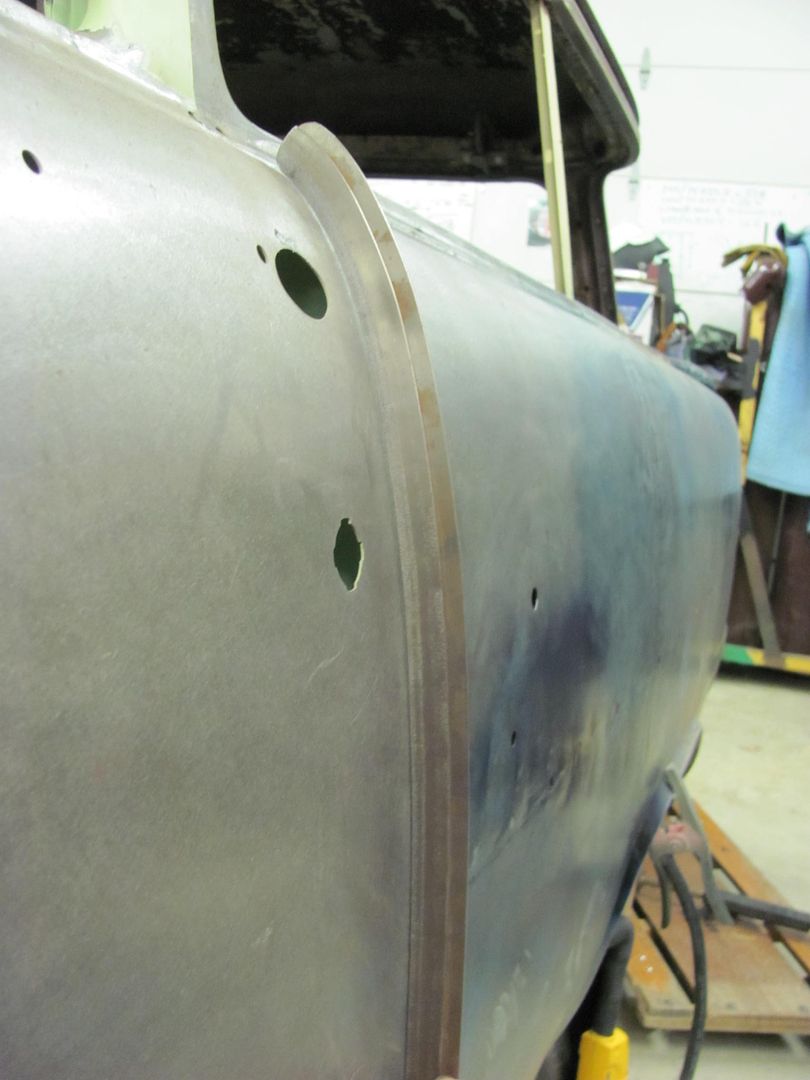
Ends are radiused...
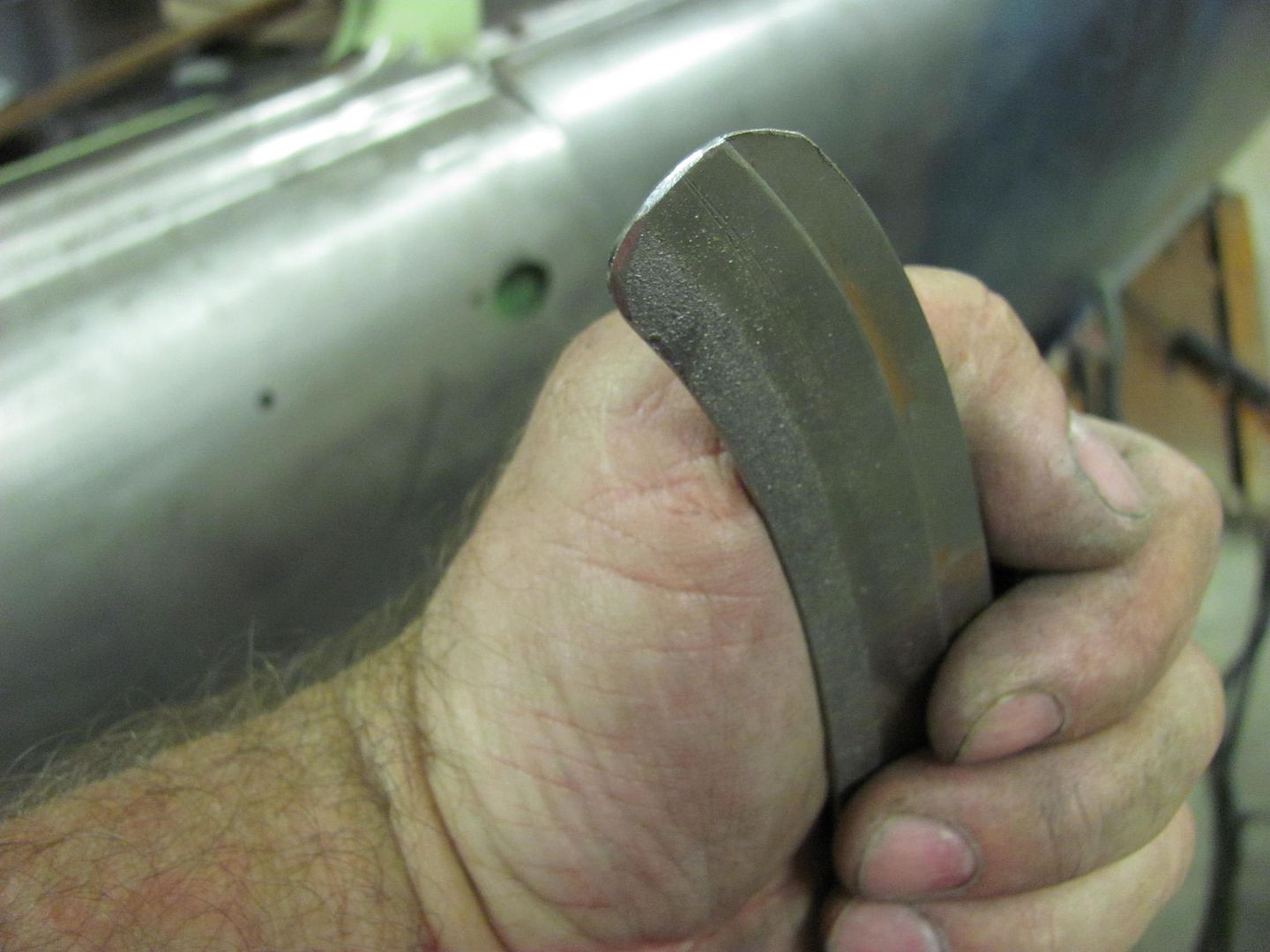