MP&C
Member
Yes and no. The biggest problem in using the Mig is all the work in planishing and grinding the welds. Using Tig or O/A will normally give you a weld with slightly less proud, for less cleanup. They also require a bit more manual dexterity in controlling the heat, controlling the puddle, adding filler, etc. So if you can't walk and chew gum... the "point and shoot" of a mig may be a better solution. (I'm still practicing... with the Tig and the gum
) But hands down, the method that requires the least amount of cleanup afterward would be a fusion weld (adding no filler) using the Tig or O/A. Either will require an absolutely tight joint. So to be effective, you'll have much more time in panel fitment to get the gaps non-existent. Here's some fusion weld practice I did using Tig, the first step is to tack the panels together. Using no filler, electrode about 1/16 away, a quick zap, one second or less, will tack the panels. Note the minimal HAZ.
Here's a practice piece I did in fusion welding, this is done with the heat dial set slightly higher than if using filler, mash the pedal FULLY, and controlling the heat by the speed of your weld pass (faster than normal). The front shows some slight undercutting..
The rear side shows some good weld penetration in some areas and others needed a bit more heat. I need more practice
This weld could be planished if there was any deformity, filed if there were any high spots, but for the most part after a fusion weld like this you are all but done. The largest amount of deformity in any weld comes from inconsistency, and stopping and starting. With these fusion welds and one quick, continual pass, you will have the least amount of deformity of any sheet metal weld, and obviously, the least amount of cleanup work after..
Just to show that slight undercutting on fusion welding was not an issue in the joint's strength, the seam was clamped in the apron brake and bent to 135 degrees, with no detriment to the weld..
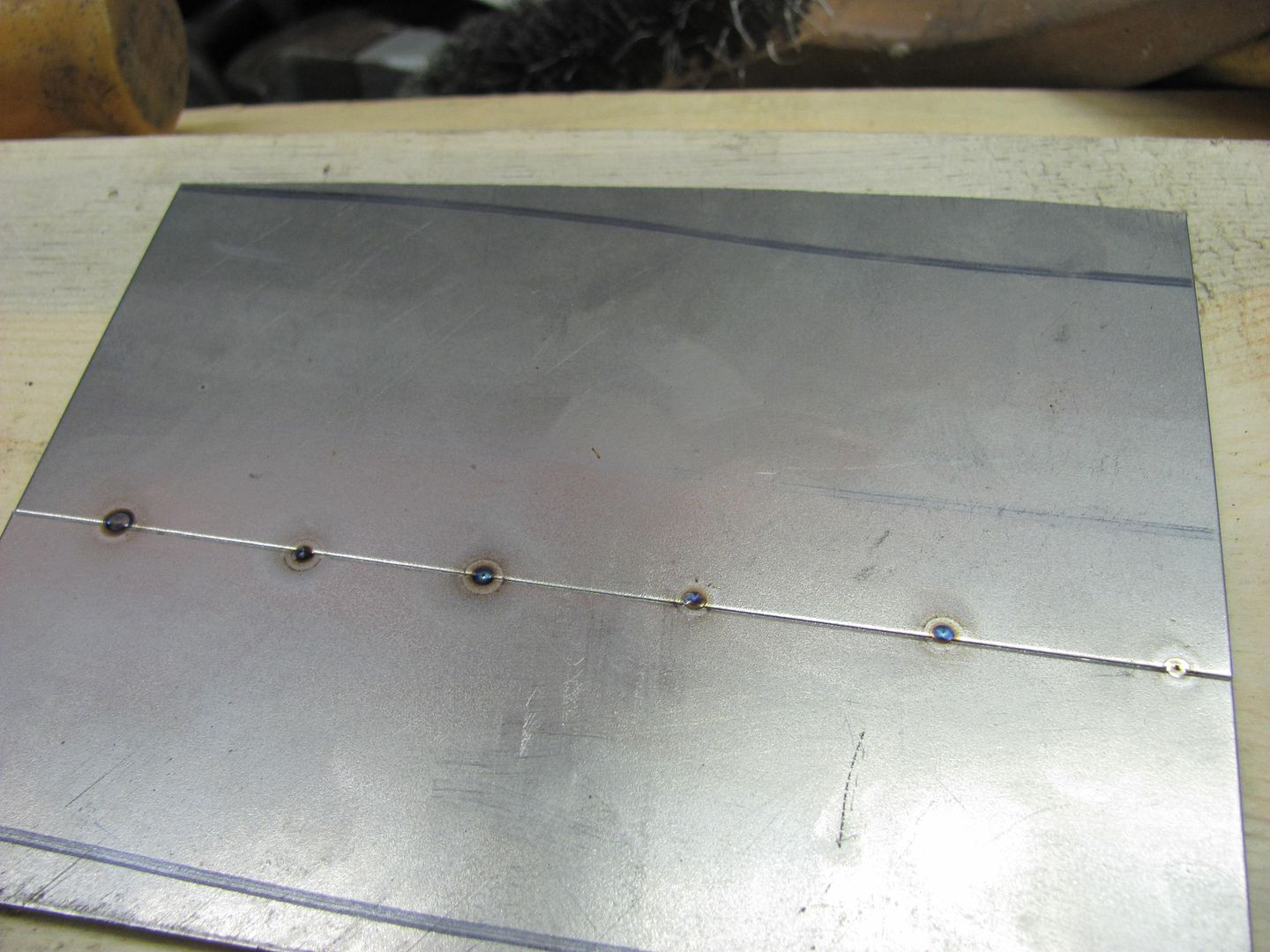
Here's a practice piece I did in fusion welding, this is done with the heat dial set slightly higher than if using filler, mash the pedal FULLY, and controlling the heat by the speed of your weld pass (faster than normal). The front shows some slight undercutting..
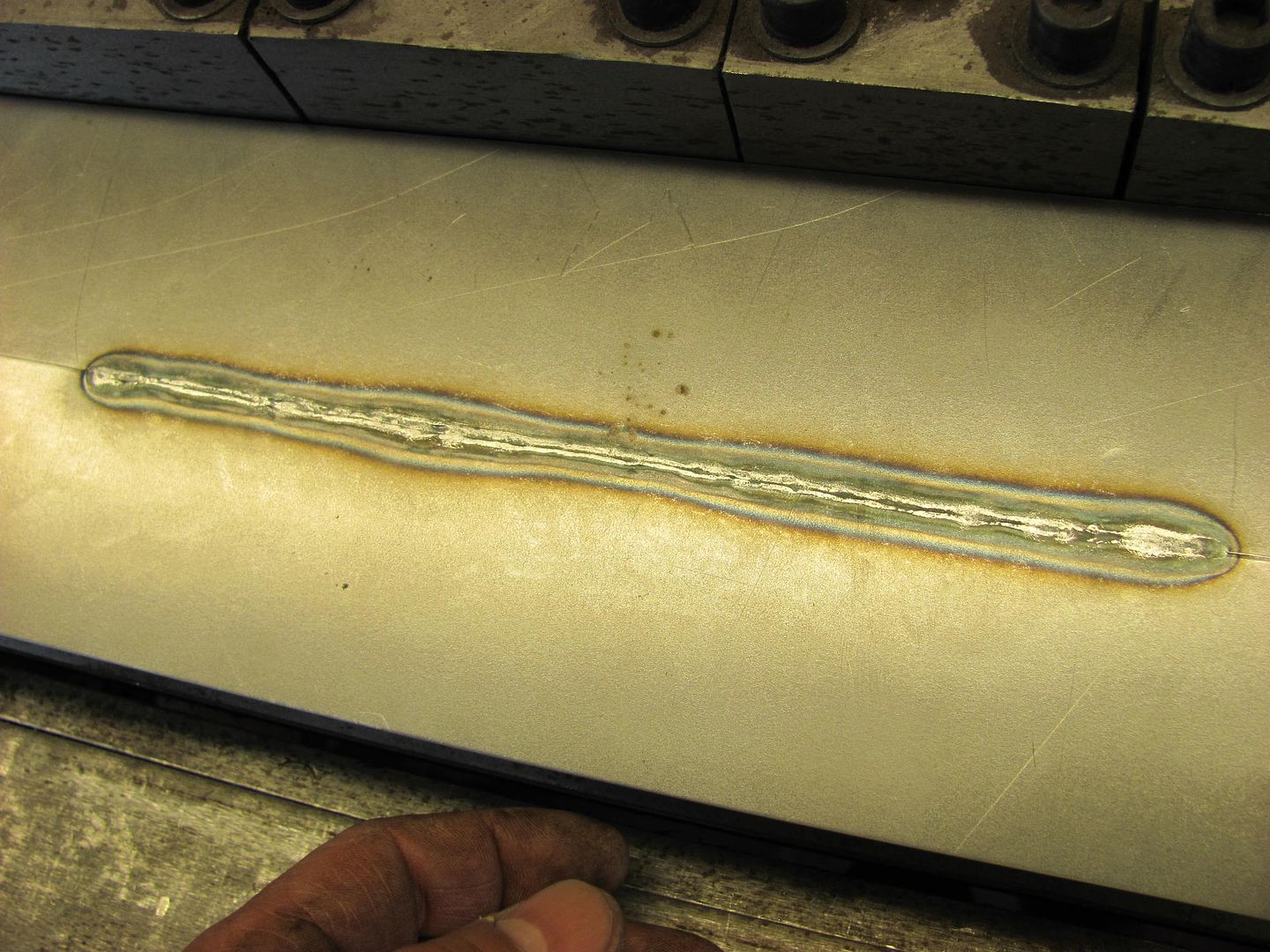
The rear side shows some good weld penetration in some areas and others needed a bit more heat. I need more practice
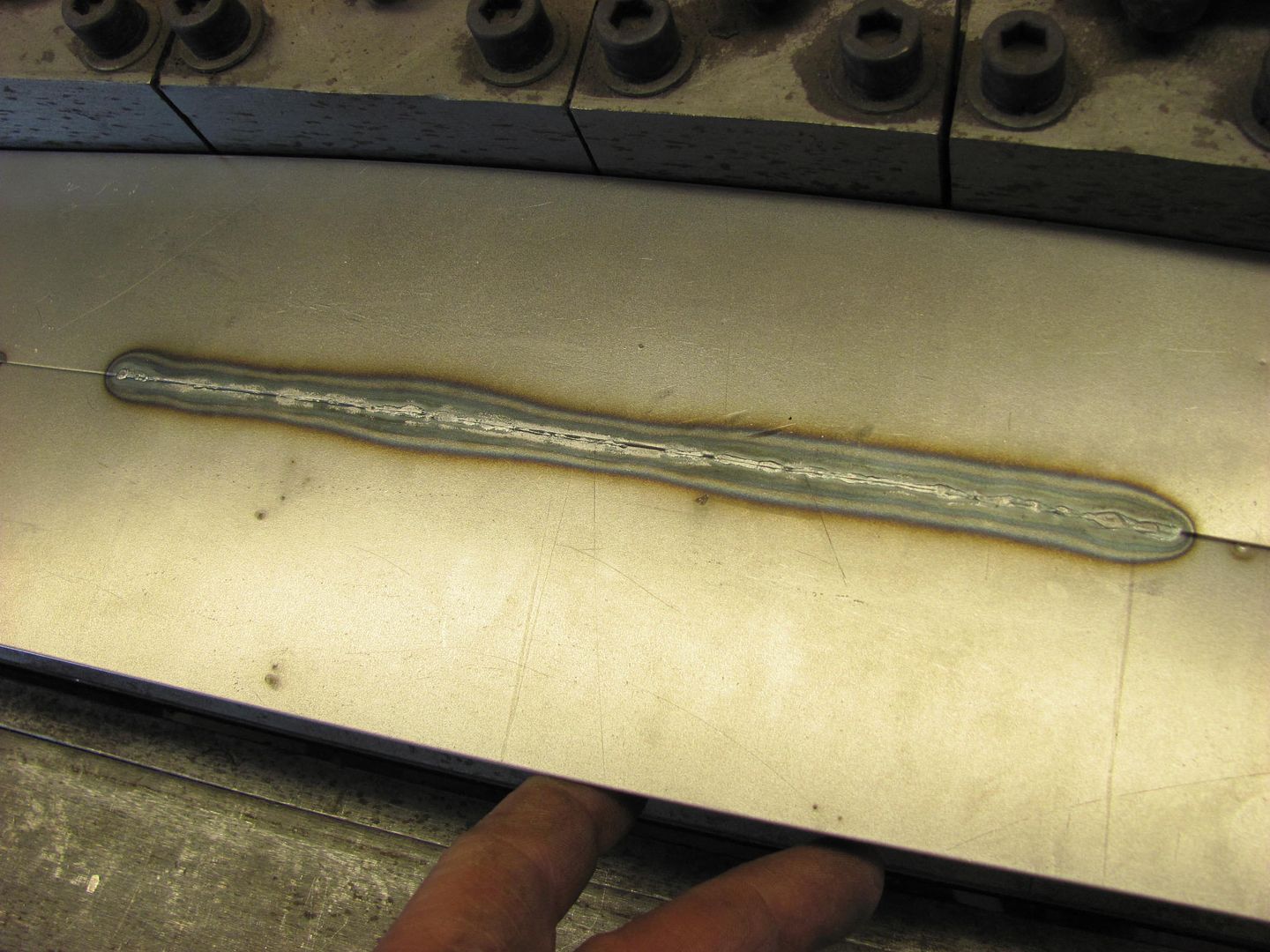
This weld could be planished if there was any deformity, filed if there were any high spots, but for the most part after a fusion weld like this you are all but done. The largest amount of deformity in any weld comes from inconsistency, and stopping and starting. With these fusion welds and one quick, continual pass, you will have the least amount of deformity of any sheet metal weld, and obviously, the least amount of cleanup work after..
Just to show that slight undercutting on fusion welding was not an issue in the joint's strength, the seam was clamped in the apron brake and bent to 135 degrees, with no detriment to the weld..
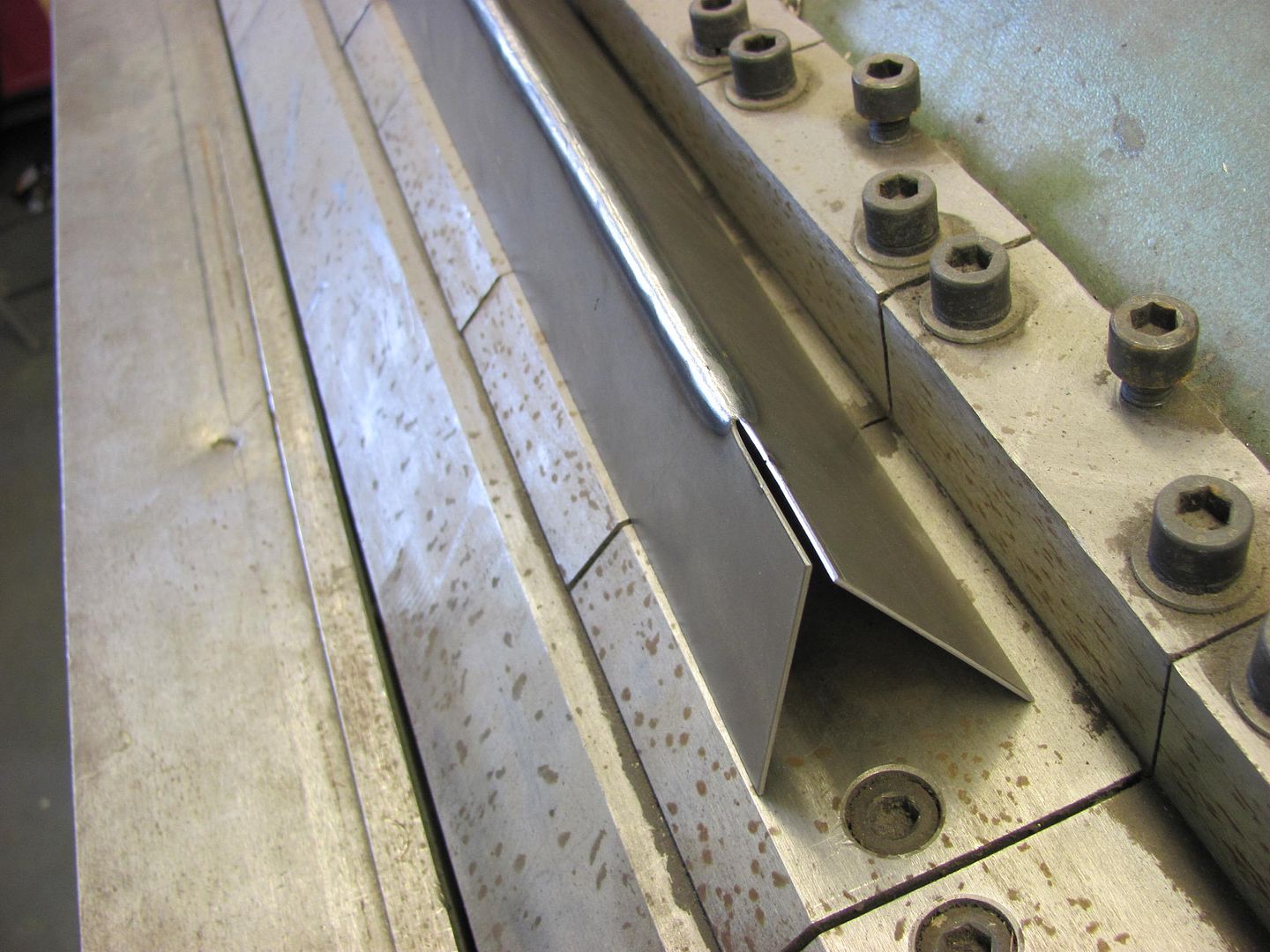
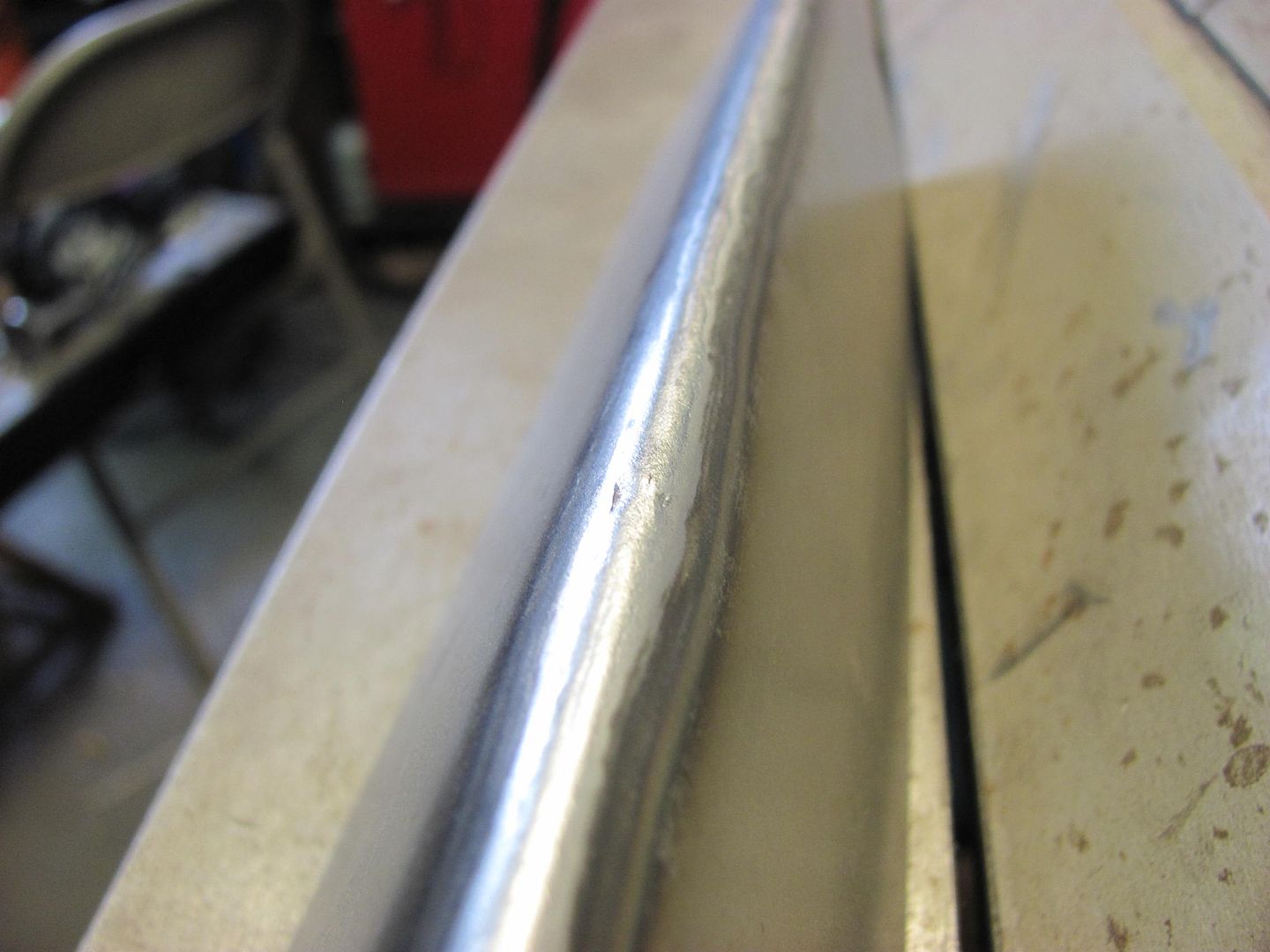