C
cstrom72
i welded in my patch panels on the rear of my Bronco project and i have a small "gully" where the weld has sunk a little in the panel. im concerned with trying to grind it flush without thinning the metal around the weld. Ive been using a flap wheel on an electric grinder and small roloc wheels on my air grinder. I have the welds roughly smoothed down but the final smoothing seems like it would take forever going the way that im trying.. I welded in two patch panels in about 5 hours using spot welds and then splitting the distance between the welds and using a little air from the compressor to cool the welds. I would do 5 or so welds and switch sides do another 5 then let them cool for a bit then repeat and I still got more warpage than I wanted but its nothing a light coat of filler wont take care of. Im just wanting to get my metal prepped just right for my epoxy then I can use a little filler to snooth the weld areas. Any tips??
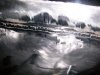
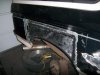
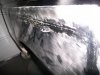
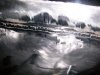
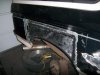
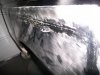